高速ロボットアーム
最高で毎分300回のショットスピードを発揮できる高速で精密なLoson社のデルタロボットは、ピッキング工程や包装工場で使用されています。TECAPEEK naturalを使用することで、食品包装向けデルタロボットの機能を向上させることができました。
CFRP: 炭素繊維複合素材(この場合、エポキシマトリックスの炭素織布)の部品は、重量と慣性の低下、金属レベルの高い機械的特性を維持するため用いられました。これまで他の機械部品に接続する際は挿入部に金属製(スチール、アルミニウム、チタンなど)を使用していたため、CFRPの軽量性のメリットを完全には発揮することができませんでした。
上の写真は、デルタロボットのロボットアームですが、以前は全重量約300 gのうち、80 g(27%)以上をアルミニウム製挿入部が占めていたため、一部において軽量化と慣性の低下は実現できておりませんでした。また、酸やアルカリが洗浄に使用されるような過酷な環境では、金属ではサビやガルバニック腐食のリスクが高くなるため、耐久性も不安でした。
挿入部:アルミニウムからプラスチックへの代替検討
プラスチックの接着
まず、アルミニウム製の挿入部を高機能プラスチックに代えることで、軽量化と腐食リスクの低減を目指すと同時に、この用途で求められる高い機械的強度を確保しようという考え方になりました。
一般的に、金属製の挿入部は二液の熱硬化性樹脂で複合素材に接着するか、または接着剤としてプラスチックを使ってCFRPフレームに直接組み込みます。
残念ながら、ポリマー製挿入部とCFRP部品との接着力では、金属と同レベルの粘着力を確保できません。表1のグラフのように、熱可塑性プラスチックの接着によって得られる剪断強度は、一般に構造部品の接着に最低限必要とされる6MPaの閾値をはるかに下回るのが一般的です。
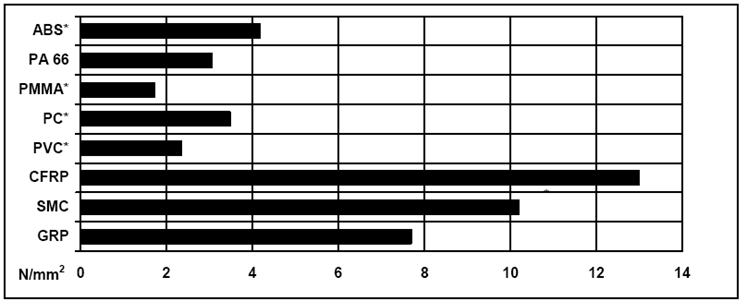
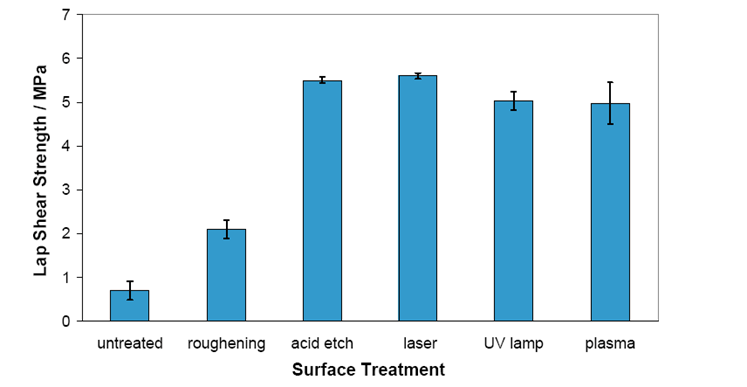
PEEK樹脂同士の接着強度
金属をプラスチックに置き換える際は、公差、構造的設計、接合など重要と思われるポイントを特定した上で、部品設計を分析し、新しい素材に合わせて見直す必要があります。金属と比べて、エポキシとPEEKの粘着力は常に小さくなります。表2はさまざまな表面処理方法でのPEEK同士の接着を示します。表面処理を施さずに接着した場合、最も強度が低くなることがわかります(グラフの一番左のuntreated)。
設計の変更
図1のように、当初の高速ロボットアーム挿入部の設計ではCRFPマトリックスに安全に固定できず、挿入部とアームの間で回転してずれる危険性がありました。
接着性の低さを克服し、部品のずれを避けるために、TECAPEEK natural製挿入部とCFRP部品との間に機械的接合設けることで検討が進められました。
図2の断面に示すように、TECAPEEK natural製挿入部にくり抜き(アンダーカット)施し、CFRP部品との密着性を向上させたことでフィットするようになりました。
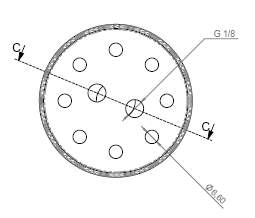
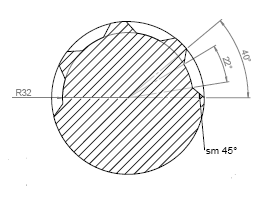
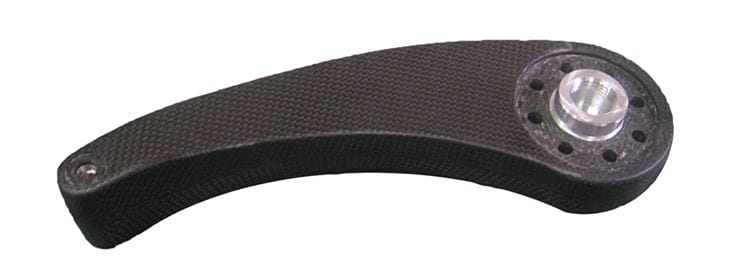
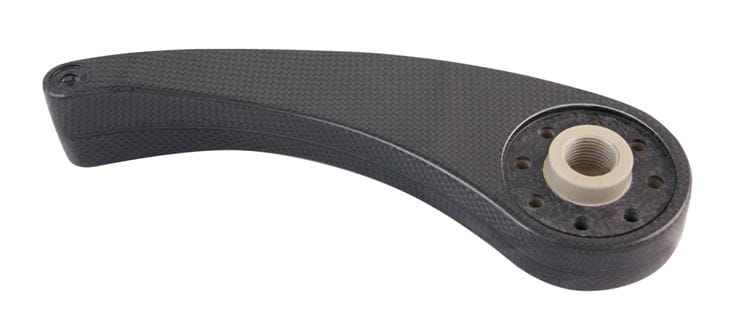
従来の高速ロボットアームからの置換えソリューションにより、以下の効果を得ることができました。
- アルミニウムから高機能プラスチック(TECAPEEK natural)への変更により軽量化。
- 機械加工したアンダーカット部にCFRPを直接はめ込むなど、部品設計をアップグレードし接着剤の使用を回避。部品の不意な回転によるずれを防止。
- 金属を使用しないことによるガルバニック腐食とサビの回避。
このソリューションにより部品の総重量がさらに15%ほど減り、慣性モーメントが低下したことでデルタロボットをより速く安全に操作できるようになりました。
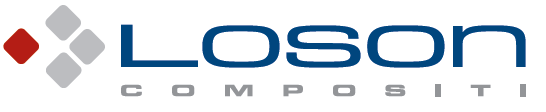