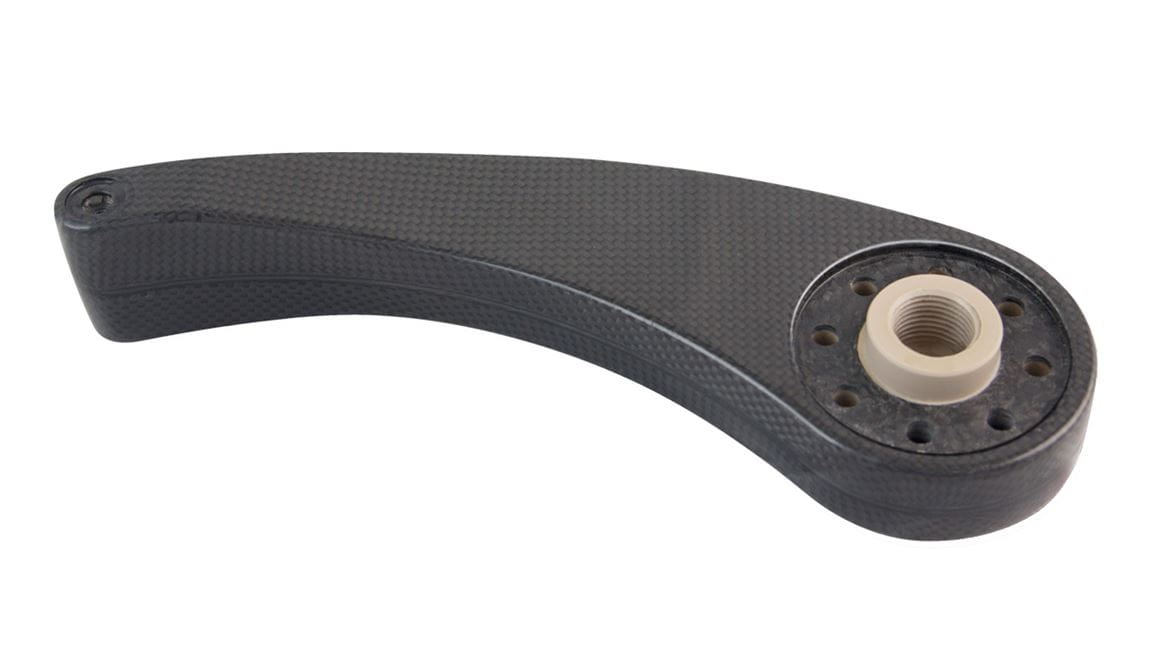
Composiet robotarm
In deze casestudie werkten Loson en Ensinger mee aan de verbetering van de prestaties van een robotarm die gebruikt wordt in een Delta-robot voor verpakkingslijnen van levensmiddelen. Dergelijke snelle en nauwkeurige machines worden in fabrieken gebruikt voor het verzamelen en verpakken dankzij hun snelheid, die het in sommige gevallen mogelijk maakt om tot 300 picks per minuut uit te voeren.
Koolstofvezel composiet onderdelen (in dit geval koolstofgeweven stof in een epoxy matrix) zijn ontworpen en geproduceerd om gewicht en traagheid te verminderen, met behoud van hoge mechanische eigenschappen die typisch zijn voor hoogwaardige metaallegeringen. Hoewel lichtheid een van de belangrijkste eisen is, zijn zware metalen inserts (staal, aluminium of, in enkele gevallen, titanium) normaal gesproken nodig om koolstofvezel composiet onderdelen aan te sluiten op andere mechanische componenten, waardoor het voordeel van de koolstofvezel gedeeltelijk wordt verminderd.
Figuur. 1 toont een robotarm voor een machine in de voedingsmiddelenverpakkingsindustrie: van een totaalgewicht van ongeveer 300 g wordt meer dan 80 g (27%) voor rekening genomen door aluminium inzetstukken, zodat de inspanning om het gewicht van het onderdeel te verminderen gedeeltelijk in het gedrang komt. Ook in ruwe omgevingen, waar agressieve zuren/basen worden gebruikt voor het reinigen (bijvoorbeeld voedselverpakkingslijnen), is deze configuratie onderhevig aan een hoog risico van zout corrosie of corrosie van de galvanische koppeling.
Aluminium
Het idee is om een inzetstuk van aluminium (of een ander metaal, en dus nog zwaarder) te vervangen door een hoogwaardige kunststof om gewicht te verminderen het risico van corrosie te verminderen, en tegelijkertijd de hoge mechanische prestaties te garanderen die nodig zijn voor de toepassing.
Metalen inlegdelen worden over het algemeen met twee-componenten epoxy lijmen op composietdelen verlijmd, of worden rechtstreeks in het composietframe verwerkt met behulp van de hars.
Helaas kan de hechtkracht tussen een polymeer-inzetstuk en het composietdeel, gezien de literatuur, niet dezelfde adhesie garanderen, zoals bijvoorbeeld in tabel nr.1 is te zien. Dit diagram laat zien dat de schuifsterkte van een verbinding door het verlijmen van verschillende thermoplastische polymeren in het algemeen ver onder de drempel van 6 MPa ligt, die algemeen beschouwd wordt als het minimum voor "structurele" hechting.
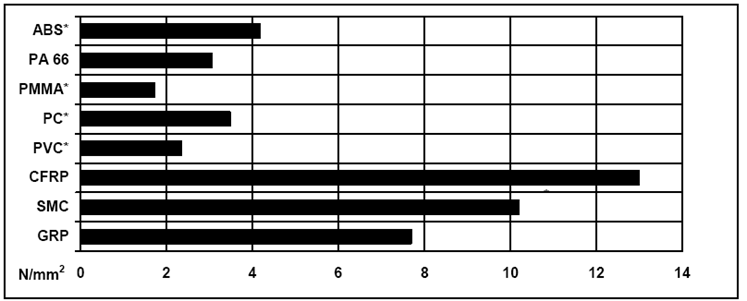
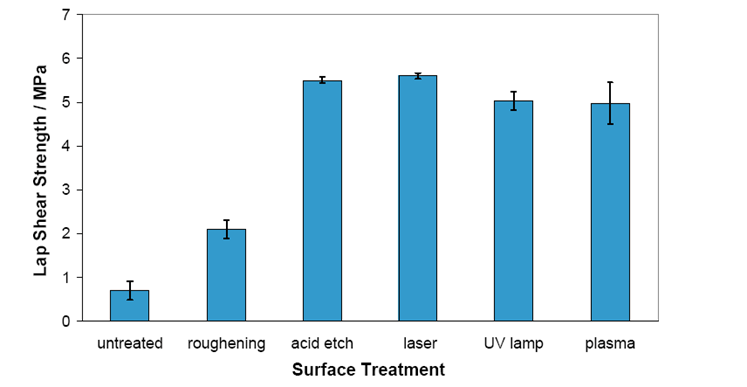
Zoals altijd, bij het vervangen van een metaal door een kunststof, moet het ontwerp van de componenten worden geanalyseerd en aangepast aan het nieuwe materiaal na het identificeren van mogelijke kritische aspecten zoals toleranties, ontwerp enhechting.
De hechting van epoxy op PEEK is altijd veel lager dan op metaal. Bijvoorbeeld, tabel n. 2 toont de PEEK op PEEK verlijming met verschillende oppervlaktebehandelingen en onder diverse omstandigheden, en onderstreept de lage prestaties van verlijmde kunststofoppervlakken.
In het geval van deze composiet robotarm heeft het oorspronkelijke ontwerp geen veilige hechting van de component aan de CRFP-matrix opgeleverd, met het risico van relatieve rotatie tussen de insert en de arm.
Om de lage prestaties van de lijm te overwinnen en de relatieve rotatie van de componenten te vermijden, werd een mechanische verbinding tussen TECAPEEK naturel insert en koolstofvezel composiet onderdeel ontworpen en gefabriceerd. Zoals blijkt uit de dwarsdoorsnede in tekening nr.2, worden sommige inkervingen in het TECAPEEK naturel inzetstuk gefreesd, zodat dat tijdens het lamineringsproces veilig in het koolstofvezelcomposietdeel kan worden verwerkt. De inkervingen van de inzetstukken zijn volledig gevuld met het gelamineerde composietmateriaal om relatieve rotatie van de twee componenten te vermijden.
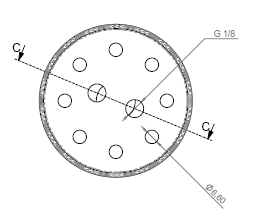
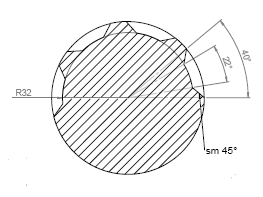
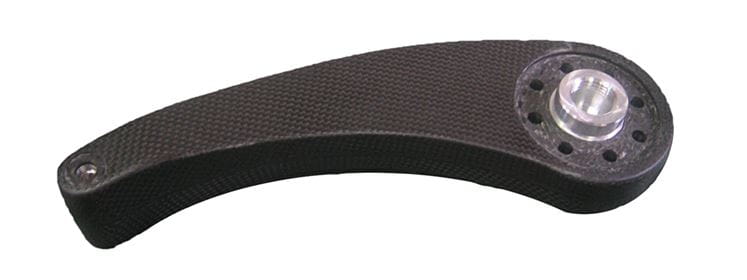
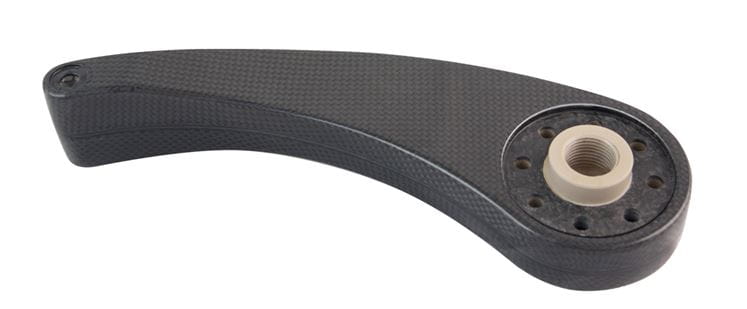
Een perfect uitwisselbare oplossing voor de originele composiet robotarm werd ontwikkeld. De component werd versterkt door:
- Gebruik van inlegdelen gefabriceerd van hoogwaardig kunststof (TECAPEEK natural), die de verhouding tussen de prestaties en het gewicht van de assemblage in vergelijking met aluminium inlegdelen doet toenemen.
- Upgrade van het componentontwerp inclusief machinaal bewerkte inkepingen, rechtstreeks gevuld met de composietmatrix tijdens de lamineringsprocedure, om het gebruik van de lijm te vermijden. Deze oplossing voorkomt ongewenste relatieve rotatie van de componenten.
- Bescherming tegen galvanische en chemische corrosie dankzij de afwezigheid van metalen.
Met deze oplossing werd het totale gewicht van het onderdeel verder verminderd met bijna 15%, waardoor de Delta-robot theoretisch sneller en veiliger kan werken dankzij het lagere traagheidsmoment.
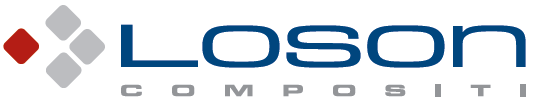