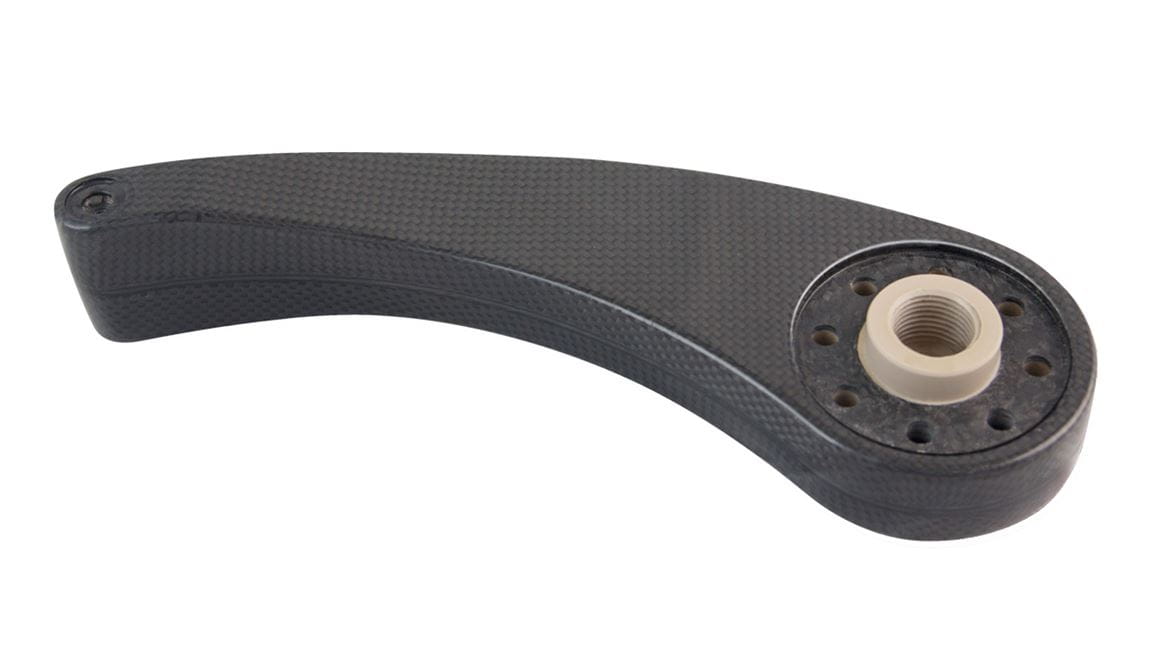
Roboterarm aus faserverstärktem Kunststoff
In dieser Fallstudie arbeiteten Loson und Ensinger zusammen, um die Leistung eines Roboterarms zu verbessern, der in einem Delta-Roboter in Verpackungsstraßen für Lebensmittel zum Einsatz kommt. Diese schnellen und präzisen Maschinen werden in Werken für die Aufnahme und Verpackung eingesetzt. Dank ihrer Geschwindigkeit können in einigen Fällen sogar bis zu 300 Aufnahmen pro Minute erreicht werden.
Bauteile aus mit Kohlenstofffasern verstärkten Kunststoffen (in diesem Fall Kohlefasergewebe in einer Epoxid-Matrix) werden entworfen und hergestellt, um Gewicht und Trägheit zu reduzieren und die mechanischen Eigenschaften aufrechtzuerhalten, die für hochwertige Metalllegierungen typisch sind. Auch wenn Leichtigkeit zu den wichtigsten Zielen gehört, müssen dennoch schwere Metalleinsätze (Stahl, Aluminium oder, in einigen Fällen, Titan) verwendet werden, um die mit Kohlenstofffasern verstärkte Kunststoffteile mit anderen mechanischen Komponenten zu verbinden. Die Vorteile der Kohlenstofffasern werden daher teilweise reduziert.
Abb. 1 zeigt einen Roboterarm für eine Verpackungsmaschine in der Lebensmittelindustrie. Bei einem Gesamtgewicht von 300 g entfallen mehr als 80 g (27 %) auf Aluminiumeinsätze. Daher wird das Ziel der Gewichtsreduktion des Teils (zur Reduzierung der Trägheit) teilweise aufgehoben. In rauen Umgebungen, wo aggressive Säuren/Basen für Reinigungszwecke verwendet werden (z. B. in Verpackungsstraßen für Lebensmittel), besteht bei dieser Konfiguration ein hohes Risiko der Salzkorrosion oder galvanischen Kupplungskorrosion.
Aluminium
Die Idee bestand darin, einen aus Aluminium (oder einem anderen und damit noch schwereren Metall) hergestellten Einsatz durch einen Einsatz zu ersetzen, der aus einem Hochleistungspolymer hergestellt wurde. So sollten das Gewicht und das Korrosionsrisiko reduziert und die durch die Anwendung geforderte hohe mechanische Leistung sichergestellt werden.
Metalleinsätze werden in der Regel mithilfe von Zweikomponentenklebstoffen aus Epoxid an Verbundteile verklebt oder direkt in den Verbundrahmen integriert, wobei das Harz der Polymermatrix als Klebemittel verwendet wird.
Leider kann der Literatur entnommen werden, dass die Klebfestigkeit zwischen einem Polymereinsatz und einem Verbundwerkstoffteil nicht dieselbe Adhäsionsstärke bieten kann, wie die in Tabelle 1 dargestellten Beispiele. Das Diagramm zeigt, dass die Scherkraft einer Verbindung, die durch Verklebung verschiedener Thermoplaste entsteht, in der Regel deutlich unter dem Grenzwert von 6 MPa liegt, der allgemein als Mindestgröße für eine „strukturelle“ Verklebung betrachtet wird.
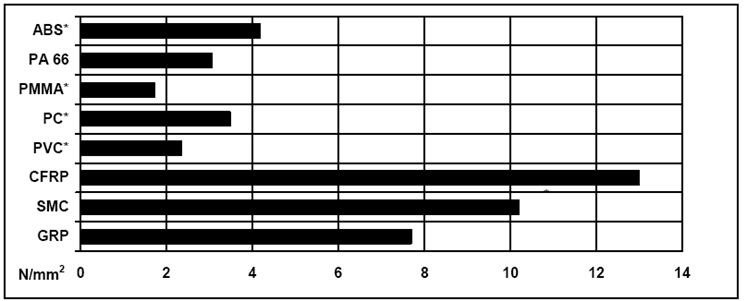
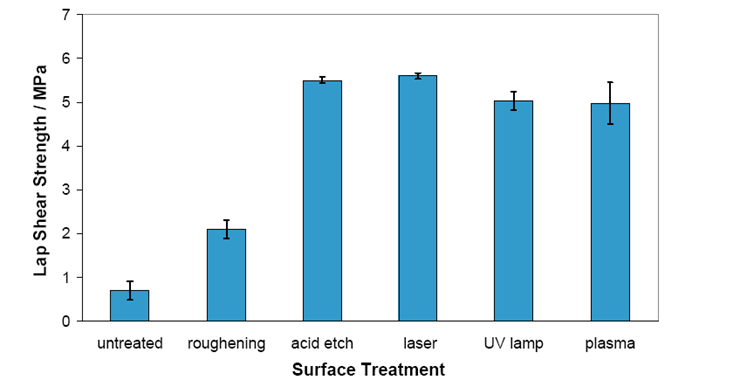
Auch hier muss beim Austausch von Metallen durch Kunststoffe das Design der Komponenten analysiert und an den neuen Werkstoff angepasst werden. In diesem Zusammenhang sind speziell potenziell kritische Aspekte wie Toleranzen, das Strukturdesign und Verbindungen zu ermitteln.
Die Adhäsion von Epoxiden an PEEK ist immer deutliche schwächer als bei Metallen. Tabelle 2 zeigt beispielsweise die PEEK-PEEK-Verklebung mit verschiedenen Oberflächenbehandlungen und unter verschiedenen Bedingungen. Damit wird die schwache Leistung verklebter Polymerflächen unterstrichen.
Im Fall dieses Roboterarms aus faserverstärktem Kunststoff führte das ursprüngliche Design des Einsatzes nicht zu einer sicheren Befestigung der Komponente an der CRFP-Matrix. Daher bestand das Risiko einer relativen Rotation zwischen Einsatz und Arm.
Um das Defizit des Klebstoffs wettzumachen und die relative Rotation der Komponenten zu vermeiden, wurde eine mechanische Verbindung zwischen dem Einsatz aus TECAPEEK natural und dem Bauteil aus mit Kohlenstofffasern verstärktem Kunststoff entworfen und produziert. In dem in Abb. 2 dargestellten Querschnitt ist zu erkennen, dass Unterschnitte in den Einsatz aus TECAPEEK natural eingebracht wurden, damit dieser bei der Laminierung sicher in das Kohlefaserbauteil eingesetzt werden kann. Die Unterschnitte der Einsätze werden vollständig mit dem laminierten Verbundwerkstoff gefüllt, um eine relative Rotation der beiden Komponenten zu vermeiden.
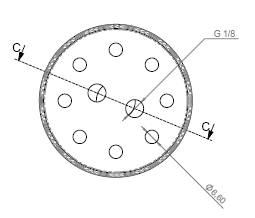
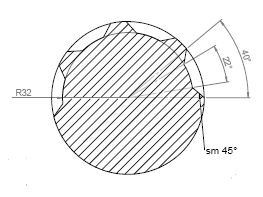
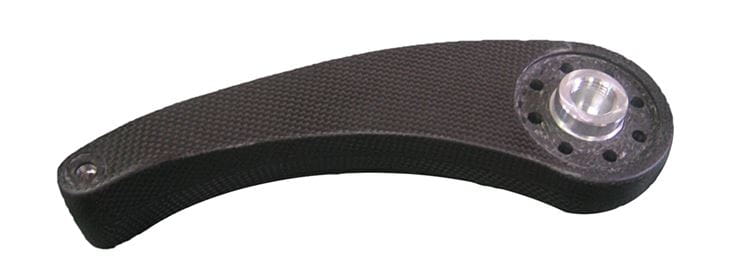
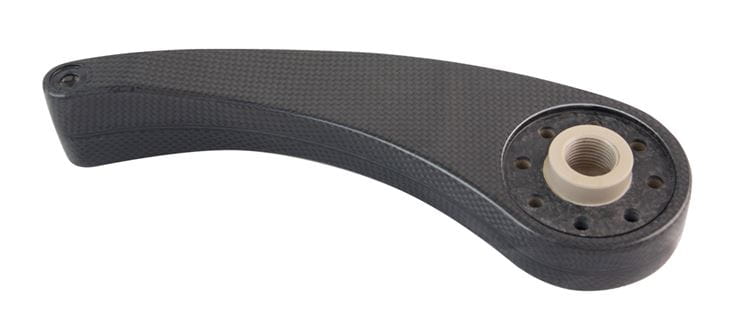
Damit wurde eine perfekte, austauschbare Lösung für den ursprünglichen Roboterarm aus faserverstärktem Kunststoff entwickelt. Die Komponente wurde verbessert durch:
- die Verwendung von Einsätzen, die aus Hochleistungskunststoff hergestellt wurden (TECAPEEK natural), wodurch das Leistungs-/Gewichtsverhältnis der Baugruppe im Vergleich zu Aluminiumeinsätzen verbessert wurde
- die Erweiterung des Komponentendesigns um eingearbeitete Unterschnitte, die bei der Laminierung direkt mit der Verbundwerkstoffmatrix gefüllt werden, um die Verwendung von Klebstoff zu vermeiden. Bei dieser Lösung wird die ungewünschte relative Rotation der Komponenten vermieden.
- den Schutz gegen galvanische und chemische Korrosion, da keine Metalle enthalten sind
Bei dieser Lösung wurde das Gesamtgewicht des Teils weiterhin um fast 15 % reduziert, was aufgrund des geringeren Trägheitsmoments theoretisch eine größere Geschwindigkeit und mehr Sicherheit beim Betrieb des Delta-Roboters bewirken sollte.
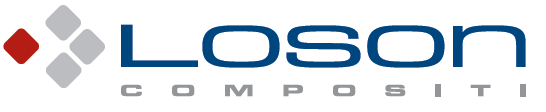