Brazo robótico de composite
En este caso práctico, Loson y Ensinger colaboraron para mejorar el rendimiento de un brazo robótico utilizado en un robot Delta para líneas de envasado de alimentos. Este tipo de máquinas rápidas y precisas se utilizan para coger y embalar productos en las fábricas, ya que gracias a su velocidad pueden, en algunos casos, realizar hasta 300 operaciones por minuto.
Las piezas de composite con fibra de carbono (en este caso carbono tejido en una matriz epoxi) se diseñan y fabrican para reducir el peso y la inercia, pero conservan las buenas propiedades mecánicas típicas de las aleaciones metálicas de alta calidad. Aunque la ligereza es uno de los principales objetivos, normalmente se necesitan pesados insertos de metal (acero, aluminio o, en algunos casos, titanio) para conectar las piezas de composite de fibra de carbono con otros componentes mecánicos, lo que reduce parcialmente las ventajas de la fibra de carbono.
En la figura 1 se ve un brazo robótico para una máquina de envasado de alimentos: de un peso total de 300 g aproximadamente, más de 80 g (27 %) corresponden a insertos de aluminio, lo que contrarresta en parte el objetivo de reducir el peso de la pieza (para reducir la inercia). Además, en entornos duros en los que se utilizan ácidos/bases agresivos para la limpieza (por ejemplo, en líneas de envasado de alimentos), esta configuración está expuesta a un elevado riesgo de corrosión por sales o por acople galvánico.
Aluminio
La idea es sustituir un inserto de aluminio (o de otro metal todavía más pesado) por un polímero de altas prestaciones para reducir el peso y el riesgo de corrosión y, al mismo tiempo, garantizar las altas prestaciones mecánicas que requiere la aplicación.
Normalmente los insertos de metal se pegan a las piezas de composite utilizando pegamentos epoxi bicomponente o se incorporan directamente en el marco de composite utilizando la resina de la matriz polimérica como pegamento.
Por desgracia, si estudiamos la bibliografía existente, la fuerza de adhesión entre un inserto polimérico y la pieza de composite no garantiza el mismo nivel de adhesión que se ve, por ejemplo, en la tabla 1. En el gráfico se ve que la resistencia a la cizalla de una unión de diferentes polímeros termoplásticos pegados por lo general está muy por debajo del umbral de 6 MPa que normalmente se considera el mínimo para una unión «estructural».
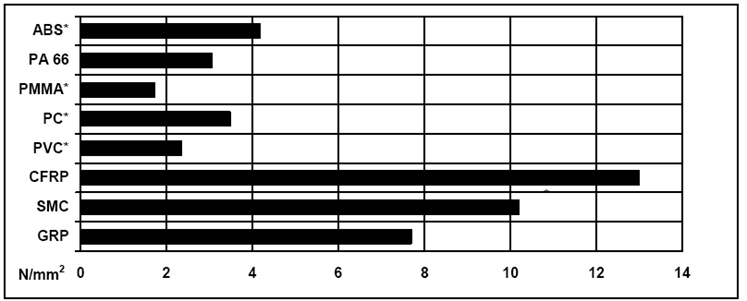
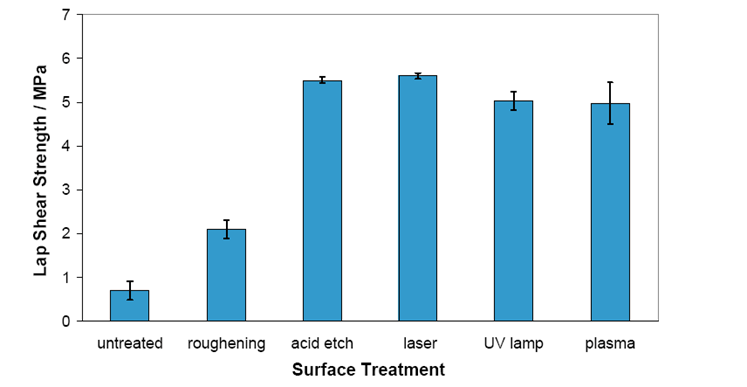
Como siempre, cuando se sustituye un metal por un plástico hay que analizar el diseño del componente para adaptarlo al nuevo material una vez identificados posibles aspectos críticos, como tolerancias, diseño estructural y uniones.
La adhesión de los epoxis al PEEK es siempre mucho peor que al metal. Por ejemplo, en la tabla 2 se puede ver el grado de adhesión de PEEK con PEEK con diferentes tratamientos superficiales y bajo distintas condiciones, destacando el mal rendimiento de la unión de las superficies poliméricas.
En el caso de este brazo robótico de plástico, el diseño del inserto original no garantizaba la adhesión segura del componente a la matriz de polímero reforzado con fibra de carbono (CRFP), por lo que existía riesgo de rotación relativa entre el inserto y el brazo.
Para compensar las deficiencias del pegamento y evitar la rotación relativa de los componentes, se diseñó y fabricó una unión mecánica entre el inserto de TECAPEEK natural y la pieza de composite de fibra de carbono. Tal y como se ve en la sección de la figura 2, en el inserto de TECAPEEK natural se mecanizaron unos rebajes para poder incorporarlo de manera segura en la pieza de composite de fibra de carbono durante el proceso de laminado. Los rebajes de los insertos quedan totalmente rellenos con el composite laminado para evitar cualquier rotación relativa de los dos componentes.
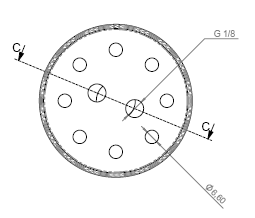
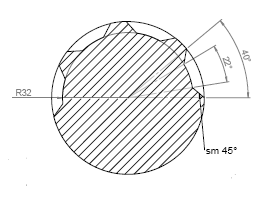
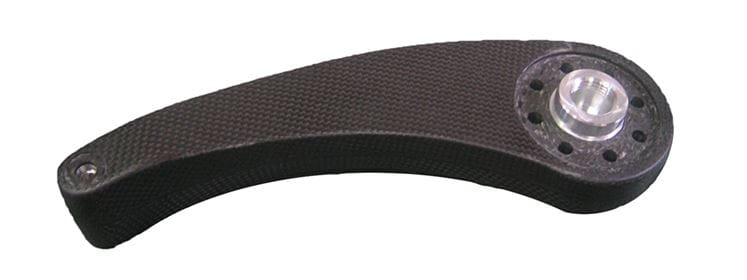
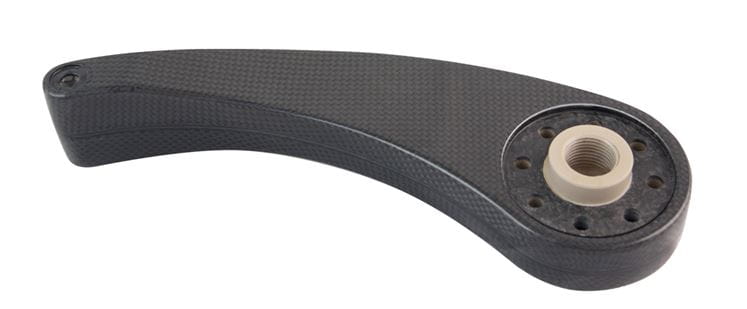
De esta forma se desarrolló una solución perfectamente intercambiable para el brazo robótico de composite original. El componente se mejoró mediante:
- Uso de insertos mecanizados de plástico de altas prestaciones (TECAPEEK natural), lo que mejoró la relación prestaciones/peso de todo el conjunto en comparación con los insertos de aluminio.
- Mejora del diseño de los componentes, que incluyó rebajes mecanizados que se rellenaron directamente con la matriz de composite durante el proceso de laminado para no tener que usar pegamento. Esta solución evita la rotación relativa no deseada de los componentes.
- Protección contra la corrosión química y galvánica gracias a la ausencia de metal.
Con esta solución, el peso total de la pieza se redujo casi en otro 15 %, lo que en teoría permite un funcionamiento más rápido y seguro del robot Delta gracias al menor momento de inercia.
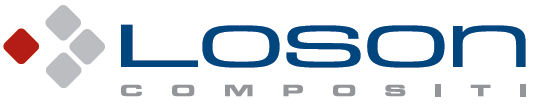