Bakery machine equipment branded and safe
In the bakery industry, the Danish company Form & Frys have found a specific niche in folding, forming and filling different products, e.g. danish pastry, pizza shells, special pies and puff pastry products. Form& Frys manufacture standard machines as well as custom-built machines, tailoring the machines to various specific customer products.
For their machines, the company wanted to use wear parts made of plastic (rollers, transport trays, folding tools, and punching plates), which could stand out colour-wise, both to brand the company, but also to ensure quick detection of any plastic fragments in the dough and thus prevent subsequent complications and recalls.
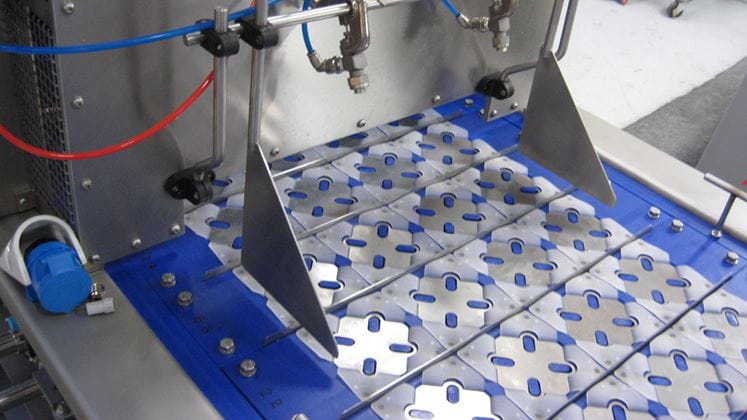
Clearly visible plastic in food
Form & Frys wanted to brand their bakery machines differently from the rest of the market, but at the same time, it was crucial for them to keep safety aspects in mind. The material should be clearly visible in the food production process, should comply with all requirements of the EU and FDA regulations regarding food contact, and at the same time, it should allow the processing of parts to complex geometries with tight tolerances and high processing and feed rates.
As the customer was looking for a material with a good level of dimensional stability, low moisture absorption, good fatigue strength and compliance with food regulations, they opted for TECAFORM AH (POM-C) and the choice was soon narrowed down to TECAFORM AH blue. This met the customers requirements for an optically detectable material and a different coloured material than the standard choice of natural or black.
Safe in every processing stage
With TECAFORM AH blue, every stage of food processing is safer, thanks to the intense blue colour of the material. Any pieces of broken plastic can be detected quickly by optical scanners or by production workers and the material also complies with EU10/2011 and FDA requirements. This is guaranteed by the use of carefully selected raw materials and material processing according to GMP 2023/2006/EU as well as the migration tests performed on Ensinger semi-finished products.
The customer not only improved the application, but also cut costs due to a massive reduction in waste and implemented an economically optimised solution, as Ensinger was able to produce the plates with dimensions of 620 x 3000 mm - the optimum size for the semi-finished material used as a starting point for the production of finished items for Form & Frys.