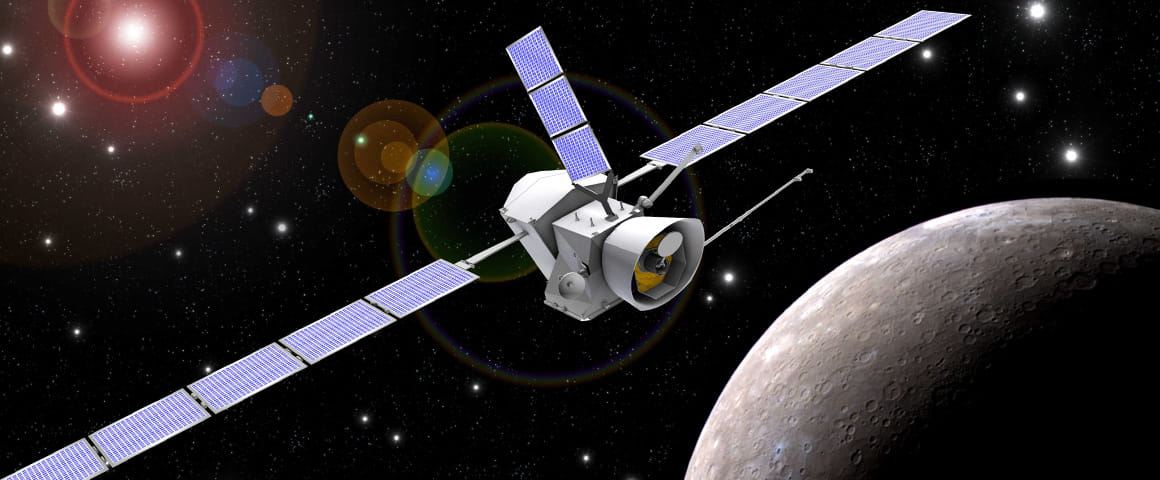
To Mercury with BepiColombo
Ensinger materials have been chosen for parts in Europe's first mission to Mercury with BepiColombo. The mission will take off on its journey to the smallest and least explored terrestrial planet in our Solar System in 2018. When it arrives at Mercury in late 2024, it will have to endure temperatures in excess of 350°C and gather data during its one year nominal mission, with a possible extension of a year.
The mission comprises of two spacecraft: the Mercury Planetary Orbiter (MPO) and the Mercury Magnetospheric Orbiter (MMO). BepiColombo is a joint mission between ESA and the Japan Aerospace Exploration Agency (JAXA), executed under ESA leadership.
Surviving the environment
The spacecraft for the mission are dependent on the function of the thermal control system (TCS), which keeps all of the spacecraft's component systems within an acceptable temperature range during every phase of the mission. It must cope with the external environment, which can vary over a wide range, as the spacecraft is exposed to deep space, solar and planetary flux. The internal heat generated by the operation of the spacecraft itself when ejecting into space also results in exposure to high temperatures.
Thermal control is essential to guarantee optimum performance and success of the mission because if a component is subjected to temperatures which are too high or too low, it could be damaged or its performance could be severely affected. Thermal control is also necessary to keep specific components (such as optical sensors and atomic clocks) within a specified temperature stability range, to ensure that they perform as efficiently as possible.
One of the components in the TCS is the thermal spacer, which is a ring-shaped plate that functions as a barrier to high temperatures and radiation. The thermal spacer has to withstand high loads and must have a very high creep resistance at high temperatures, with both properties required for a period of 6-7 years.
Maximum strength and heat resistance - TECASINT 1011
The road to an approved material for the aerospace industry and for this specific application - a thermal spacer - is long and requires thorough testing.
TECASINT 1011 was chosen for the thermal spacer as the material is non-melting and does not soften, even at temperatures up to the 350°C. The material demonstrates very low creep tendency under load, which is important for the application, as it is intended to hold a high screw force for up to 6-7 years flight time of the spacecraft. TECASINT 1011 has been tested over a period of 4-5 years by Astrium / Airbus D/S and found suitable for the application.
PolyimidE - THE MATERIAL OF CHOICE
Properties of TECASINT 1011:
- Maximum strength and elongation
- Optimum electrical insulation
- Highest modulus
- Minimal thermal conductivity
- Minimal outgassing acc. ESA Test for space applications
Other relevant applications for TECASINT 1011:
- Insulators
- Switch components
- Valve seats
- Chain guides
- Hot glass grippers
- Wear pad
- Static seals
- Wearing elements