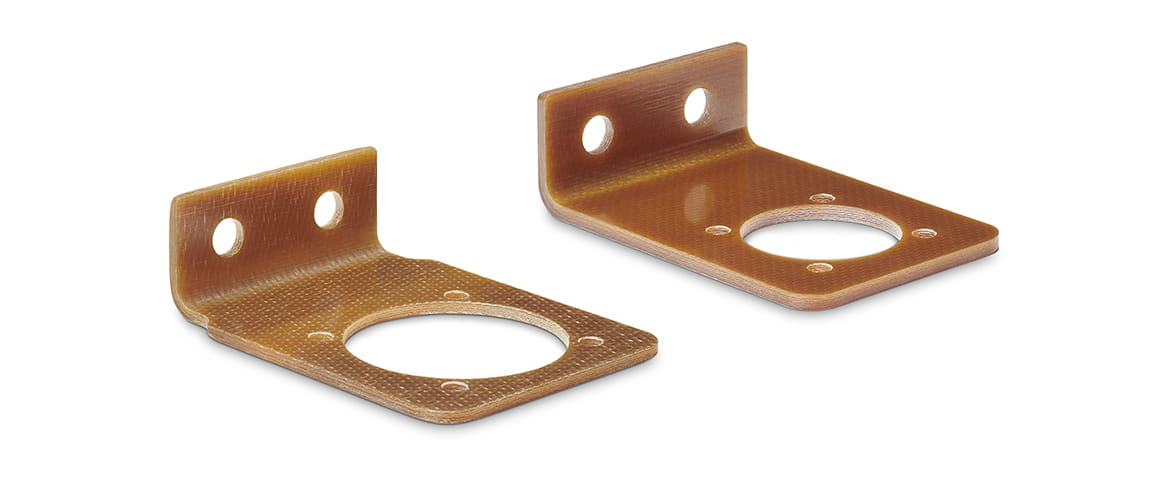
插入式電連接器固定座
飛機內裝的輕量化構造:由復合材料製作的零組件
輕量化和高強度的材料已成為航空業的高端應用中必備的材料。在客機中,每公斤都需列入計算,這就是為什麼不僅僅在飛機內裝設計中,金屬材料被越來越多被塑膠取代。尤其是熱塑性複合材料,可讓航空公司大幅減輕飛機配備的重量,而且較不會因加工限制而需做出妥協。Bucher Leichtbau和Ensinger的一個項目中顯示,使用纖維增強複合材料可以提供更多的技術優勢。
Bucher Leichtbau AG的總部位於瑞士費蘭登(Fällanden),是製造飛機內裝和汽車設備的專家。除此之外,該公司的航空部門亦開發和生產用於客機的廚房和廚櫃設備。 這種類型的組件可以承受相當於其自身重量八倍的負載,並且能夠承受至少是重力加速度九倍的加速度。 在此,區分飛行載荷(正常飛行條件,例如起飛,著陸,亂流)和緊急著陸負荷(受控的緊急著陸或中止起飛)。所生產的組件會被要求最短使用壽命,例如對於空中巴士和波音公司為25年。
最初的情況
出於安全原因,在民航客機中用於插入式電連接器的所有金屬支架必須接地。對於Bucher鋁製廚房設備中的導電支撐結構,只要配備有必要的腐蝕防護措施的現有緊固螺釘通常就足夠了。但是,如果金屬連接器固定座位於廚房設備的非導電結構上,則需要額外的電纜進行接地。該接地電纜必須定期固定,這會導致需要額外的緊固螺紋、間隔螺栓、纜夾和螺絲。
除了用於電纜線路的材料之外,規劃和安裝的成本也很高。此外除了設計電路圖外,並在測試計劃中為每條接地電纜定義電阻測量。還必須將其納入相關的維護準則和操作說明及授權文件中。在生產過程中需要記錄接觸電阻,並在每個接地連接處塗一層防腐蝕塗層。
替代使用的熱塑性複合材料無需接地連接
如果以前由金屬製成的連接器固定座替換為非導電材料,可以完全消除接地連接所涉及的工作和成本。但是,由於工作溫度和消防安全要求,無法使用低成本的標準塑料。
最廣為人知的技術替代方案需要能夠一對一地大量替換現有的鋁製零件,為了最大程度地減少引入這些零件時進行轉換時所涉及的工作和成本,需要具備剛性和高強度的材料。
由於不同連接器固定座的數量相對較少,因此無法有效解決高工具成本的方案。因此在初步試驗中,纖維增強的熱塑性型材製成的改型零件並未顯示令人滿意的結果。
然而透過恩欣格的複合材料部門的合作,很快發現了一種對於熱塑性纖維增強複合材料的合適解決方案。 由玻璃纖維和PEI(聚醚醯亞胺)製成的預浸料可用於航空工業。 短暫的優化後,便可製造出大量的零件。由於專業分工的加工技術,恩欣格的兩個據點都參與了連接器固定座的生產:
在奧特芬根(Otelfingen),恩欣格的複合材料專家使用PEI預浸料製成各種角度的半成品。與其他的零組件不同,這些胚料不是從厚板裁切一定尺寸後進行熱成型,而是使用單獨的預浸料胚層在工具中壓製成規定的形狀。除此之外,該過程具有減少回彈的優點。纖維複合材料零件的機加工處理則是在恩欣格位於巴伐利亞(Bavaria)的卡姆(Cham)的工廠進行
位於卡姆(Cham)的機加工部門為恩欣格國際機加工小組的成員之一,專門生產由熱塑性高性能塑料和復合材料製成的精密零件。
將於奧特芬根(Otelfingen)製造的各種半成品型材在卡姆進行加工,將連接器固定座加工成最終產品。
大多數的固定座會有幾種不同尺寸的規格。但因為靈活的加工技術,還可以生產出具有特殊外型或鑽孔且交貨時間短的高質量產品。
更簡單,更具成本效益,更輕便
新型塑料固定座的製造成本明顯高於以前的鋁製版本。然而,在櫥櫃設備工程和生產方面的節省,意味著新的解決方案更加簡單,並且總體上更具有成本效益。且由於使用複合材料零組件,廚房變得更輕,航空公司從長遠來看是受益的,因為不必將額外的重量都帶到空中可以節省金錢。
CNC加工之前
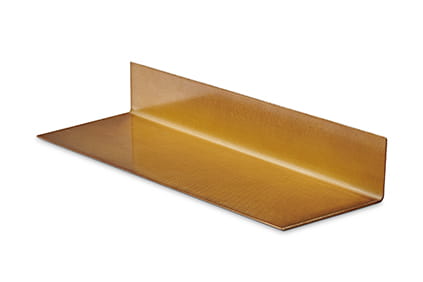
用於插入式電連接器固定座的胚料,是由複合纖維預浸料製成的。玻璃纖維和PEI(聚醚醯亞胺)製成的預浸料已被批准用於航空工業中。
連接器固定座有不同尺寸的版本。因為連續且拉直成型的纖維,熱塑性複合材料比短纖維的增強塑料具有更高的強度和剛度
預塑/預型技術
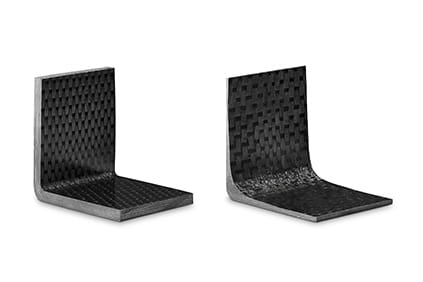
歸功於恩欣格的預塑/預型技術,在加工角度時如有壁厚的差異也是可能實現的。 因此,類似於分叉的樹枝,如是受高應力的拐角則可加固,而在不承受高應力的部分(例如,在手臂上)則可以節省材料。此製造技術被稱為“淨形成形”技術。
根據零組件的各種形狀,使用此技術可以顯著節省材料和重量,同時保持相當的強度和剛度。