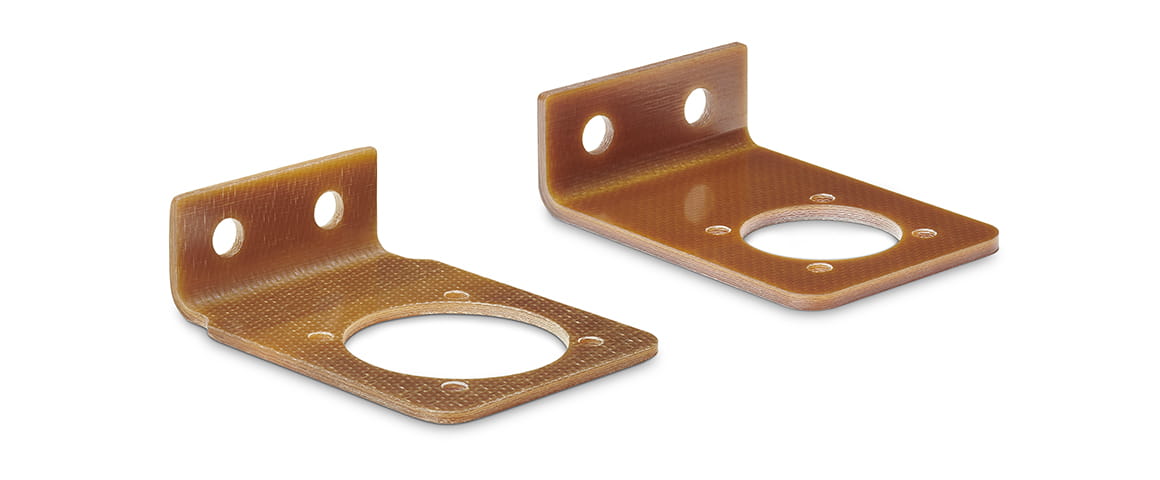
Fixadores para conexões elétricas plug-in
Componentes leves em interiores de aviões: Componentes produzidos em série com base em compósitos
Materiais leves e de alta resistência tornaram-se indispensáveis para aplicações de alto nível na indústria da aviação. Nas aeronaves de passageiros cada quilograma conta, e é por isso que os metais estão sendo cada vez mais substituídos por soluções baseadas em plásticos, também no design de interiores. Os compósitos termoplásticos, em particular, oferecem às empresas uma redução significativa do peso das aeronaves sem exigir que elas façam concessões em termos de propriedades mecânicas. Um projeto das empresas Bucher Leichtbau e Ensinger mostra que a mudança para compósitos reforçados com fibras pode proporcionar vantagens técnicas adicionais.
A Bucher Leichtbau AG, sediada em Fällanden (Suíça), é especialista em interiores de aeronaves e equipamentos automotivos. Entre outras coisas, a divisão de aviação do grupo corporativo desenvolve e produz cozinhas e armários para aeronaves de passageiros. Um módulo completo deste tipo pode acomodar uma carga correspondente a oito vezes seu próprio peso e tem que ser capaz de suportar acelerações que são pelo menos nove vezes maiores do que a aceleração gravitacional. Aqui, é feita uma distinção entre cargas de vôo (condições normais de vôo como decolagem, pouso, turbulência) e cargas de pouso de emergência (pouso de emergência controlado ou decolagem abortada). A vida operacional mínima exigida dos módulos produzidos, por exemplo, é de 25 anos para Airbus e Boeing.
SITUAÇÃO INICIAL
Por razões de segurança, todas as fixações metálicas para conexões de encaixe elétrico na aviação comercial devem ser aterradas. Com estruturas de suporte eletricamente condutivas nas cozinhas de alumínio Bucher, um parafuso de fixação existente equipado com as medidas de proteção contra corrosão necessárias é frequentemente suficiente. Se, entretanto, as fixações dos conectores metálicos forem posicionadas em estruturas não condutoras nas cozinhas, um cabo adicional é necessário para o aterramento elétrico. Este cabo de aterramento deve ser fixado em intervalos regulares, o que obriga a uma exigência de roscas de fixação adicionais, parafusos espaçadores, braçadeiras de cabo e parafusos.
Além da entrada de material para o roteamento dos cabos, surgem custos elevados para o planejamento e instalação: O trabalho de projeto inclui fazer uma entrada no diagrama esquemático do circuito; além disso, uma medida de resistência deve ser definida no plano de teste para cada cabo de aterramento. Isto também deve ser incorporado nas diretrizes de manutenção e instruções de operação relevantes, bem como nos documentos de autorização. Durante a produção, a resistência de contato deve ser registrada e um revestimento de proteção contra corrosão deve ser aplicado em cada conexão de aterramento.
O SUBSTITUTO EM COMPÓSITO TERMOPLÁSTICO ELIMINA A NECESSIDADE DE ATERRAMENTO
O trabalho e os custos envolvidos em uma aterramento podem ser completamente eliminados se as fixações do conector anteriormente feitas de metal forem substituídas por uma variante não condutora. Devido à temperatura operacional e aos requisitos de segurança contra incêndio, no entanto, não é possível utilizar um plástico padrão de baixo custo.
A alternativa técnica procurada precisava ser capaz de substituir um grande número de peças de chapa de alumínio existentes uma a uma, de modo a minimizar o trabalho e os custos envolvidos na troca quando elas foram introduzidas. Para que esta demanda seja atendida, é necessário um material rígido e de alta resistência.
Devido às quantidades relativamente pequenas de diferentes fixadores de conectores, uma solução com altos custos de ferramentas não era uma opção. Os testes iniciais com peças remodeladas localmente feitas de chapas termoplásticas reforçadas com fibra não mostraram resultados satisfatórios nas zonas remodeladas.
Trabalhando com a divisão de Compósito da Ensinger, foi rapidamente encontrada uma solução adequada com base no compósito termoplástico reforçado com fibras. Um prepreg aprovado para a indústria aeronáutica com fibra de vidro e uma matriz PEI (poliéterimida) foi escolhido para o material. Após uma breve fase de otimização, foi possível fabricar as primeiras peças produzidas em série. Devido às técnicas de processamento especializadas, duas das instalações da Ensinger estão envolvidas na produção das fixações dos conectores:
No site de Otelfingen, os especialistas em compósitos da Ensinger produzem peças semi-acabadas em forma angular a partir dos pré-impregnados da PEI. Ao contrário de componentes comparáveis, esses blanks não são cortados à medida de um laminado grosso e termoformado, mas, usando camadas individuais de pré-impregnado, prensados em uma ferramenta na forma definida. Entre outras coisas, este processo oferece a vantagem de reduzir o efeito da memória elástica. O processamento CNC das peças compostas de fibra ocorre na Ensinger GmbH em Cham, na Baviera.
O departamento de usinagem de Cham, especializado na produção de peças de precisão a partir de plásticos termoplásticos de alto desempenho e materiais compostos, é membro do grupo internacional de usinagem da Ensinger. Desde os blanks angulares produzidos em Otelfingen, a Ensinger Cham usina com precisão os fixadores de conexão até a especificação final do produto.
Para a maioria dos suportes de fixação existem várias versões com dimensões diferentes. Graças ao processo flexível, também é possível produzir desenhos especiais de alta qualidade, com contornos ou furos e com prazos de entrega curtos.
MAIS SIMPLES, MAIS ECONÔMICO E MAIS LEVE
ANTES DO PROCESSAMENTO CNC
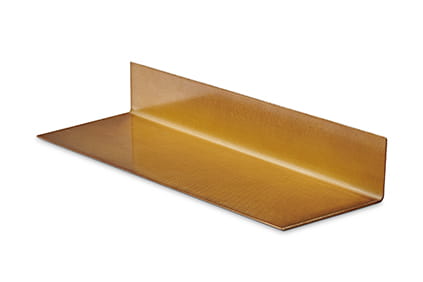
Um blank para um suporte para uma conexão plug-in é construído a partir de um pré-preg composto de fibra, aprovado para a indústria aeronáutica com fibra de vidro que está embutido em uma matriz PEI.
As fixações dos conectores vêm em versões com dimensões diferentes. Graças às fibras contínuas e endireitadas, o material compósito termoplástico tem resistência e rigidez significativamente maiores do que os plásticos reforçados com fibras curtas.
TECNOLOGIA DE PRÉ-FORMA
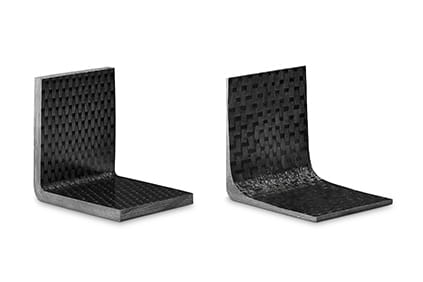
Graças à tecnologia de pré-formas da Ensinger, também são possíveis diferenças nas espessuras das paredes ao produzir ângulos. Assim, semelhante a um ramo bifurcado, a seção de canto sob altas tensões pode ser reforçada, enquanto nas seções que não estão sob altas tensões (por exemplo, sobre os braços), o material pode ser salvo. A técnica de fabricação é referida como o processo "near net shape".
Dependendo da geometria do componente, é possível economizar material e peso significativos com esta tecnologia - mantendo, ao mesmo tempo, resistência e rigidez comparáveis.