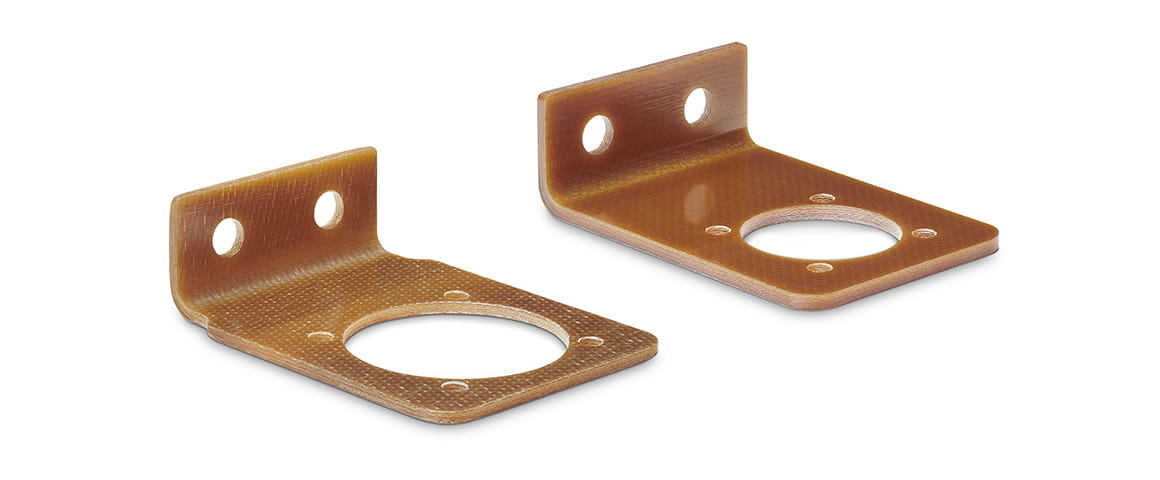
Upevnění pro elektrické zásuvné připojení
Lehká konstrukce v interiérech letadel: kompozitní sériově vyráběné komponenty
Lehké a vysoce pevné materiály se staly nepostradatelnými pro špičkové aplikace v leteckém průmyslu. V osobních letadlech se počítá každý kilogram, a proto jsou kovy stále častěji nahrazovány řešeními na bázi plastů, a to i v interiéru. Zejména termoplastické kompozity nabízejí společnostem, které dodávají letadlům, výrazné snížení hmotnosti, aniž by od nich vyžadovaly kompromisy, pokud jde o mechanické vlastnosti. Projekt společností Bucher Leichtbau a Ensinger ukazuje, že přechod na kompozity vyztužené vlákny může poskytnout další technické výhody.
Společnost Bucher Leichtbau AG se sídlem ve Fällandenu (Švýcarsko) je specialistou na interiéry letadel a automobilové vybavení. Letecká divize podnikové skupiny mimo jiné vyvíjí a vyrábí kuchyně a skříně pro osobní letadla. Celý modul tohoto typu může pojmout zatížení odpovídající osminásobku jeho vlastní hmotnosti a musí být schopen odolat zrychlení, která jsou nejméně devětkrát větší než gravitační zrychlení. Zde se rozlišuje mezi letovým zatížením (normální letové podmínky, jako je vzlet, přistání, turbulence) a nouzovým přistávacím zatížením (řízené nouzové přistání nebo přerušený vzlet). Požadovaná minimální životnost vyrobených modulů je například 25 let pro Airbus a Boeing.
výchozí situace
Z bezpečnostních důvodů musí být všechny kovové úchyty pro elektrické zásuvné spoje v komerčním letectví uzemněny. U elektricky vodivých nosných konstrukcí v hliníkových galeriích Bucher často postačuje stávající upevňovací šroub vybavený nezbytnými protikorozními opatřeními. Pokud jsou však kovové konektory umístěny na nevodivých strukturách v galeriích, je pro elektrické uzemnění zapotřebí další kabel. Tento uzemňovací kabel musí být v pravidelných intervalech zajištěn, což vyžaduje další upevňovací závity, distanční šrouby, kabelové svorky a šrouby.
Kromě vstupního materiálu pro vedení kabelů vznikají vysoké náklady na plánování a instalaci: Konstrukční práce zahrnují provedení záznamu ve schematickém schématu zapojení; navíc musí být v testovacím plánu pro každý zemnící kabel definováno měření odporu. To musí být rovněž zahrnuto do příslušných pokynů a pokynů k údržbě a do autorizačních dokumentů. Během výroby musí být zaznamenán kontaktní odpor a při každém uzemnění musí být nanesen antikorozní nátěr.
Termoplastická kompozitní náhrada odstraňuje potřebu uzemnění
Práce a náklady spojené se zemním spojením lze zcela vyloučit, pokud jsou upevňovací prvky konektorů dříve vyrobené z kovu nahrazeny nevodivou variantou. Vzhledem k požadavkům na provozní teplotu a požární bezpečnost však není možné použít levný standardní plast.
Vyhledávaná technická alternativa musela být schopna nahradit velké množství stávajících plechových hliníkových dílů jedna za druhou, aby se minimalizovala práce a náklady spojené s přechodem při jejich zavedení. Aby bylo možné tento požadavek splnit, je vyžadován tuhý, vysoce pevný materiál.
Vzhledem k relativně malému množství různých upevnění konektorů nebylo řešení s vysokými náklady na nástroje možné. Počáteční pokusy s místně remodelovanými díly vyrobenými z vlákny vyztuženého termoplastického listového materiálu neprokázaly uspokojivé výsledky v remodelovaných zónách.
Ve spolupráci s divizí Ensinger's Composite bylo rychle nalezeno vhodné řešení na bázi kompozitu vyztuženého termoplastickými vlákny. Pro materiál byl vybrán prepreg schválený pro letecký průmysl se skleněnými vlákny a PEI matricí (polyetherimid). Po krátké optimalizační fázi bylo možné vyrobit první sériově vyráběné díly. Z důvodu speciálních technik zpracování jsou do výroby konektorových spojů zapojeny dva weby společnosti Ensinger:
V Otelfingenu vyrábějí kompozitní experti společnosti Ensinger polotovary v úhlovém tvaru z prepregů PEI. Na rozdíl od srovnatelných komponent nejsou tyto polotovary vyříznuty na velikost z tlustého laminátu a tepelně tvarovány, ale pomocí jednotlivých vrstev prepregu jsou lisovány nástrojem do definované formy. Tento proces mimo jiné nabízí výhodu spočívající ve snížení efektu zpětného rázu. CNC zpracování vláknitých kompozitních dílů probíhá v Ensinger GmbH v bavorském Chamu.
Oddělení obrábění Cham, které se specializuje na výrobu přesných dílů z termoplastických vysokovýkonných plastů a kompozitních materiálů, p je členem mezinárodní skupiny pro obrábění Ensinger. Od úhlových polotovarů vyrobených v Otelfingenu provádí přesné strojní zpracování Ensinger Cham upevnění konektorů podle specifikace konečného produktu.
Pro většinu upevňovacích konzol existuje několik verzí s různými rozměry. Díky flexibilnímu procesu je také možné vyrábět vysoce kvalitní, speciální designy s obrysy nebo vyvrtanými otvory a s krátkými dodacími lhůtami.
jednodušší, nákladově efektivnější a lehčí
před CNC zpracováním
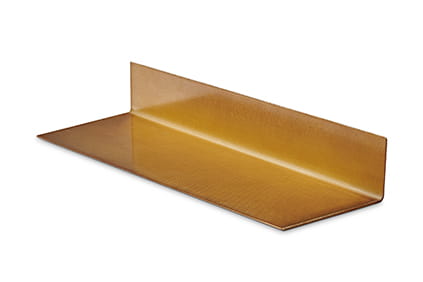
Polotovar pro držák pro zásuvné připojení je vyroben z vláknitého kompozitního předpřipraveného materiálu, schváleného pro letecký průmysl se skleněnými vlákny, které jsou zality v PEI matrici.
Upevnění konektorů se dodává ve verzích s různými rozměry. Díky spojitým, narovnaným vláknům má termoplastický kompozitní materiál výrazně vyšší pevnost a tuhost než plasty vyztužené krátkými vlákny.
TECHNOLOGie předlisku
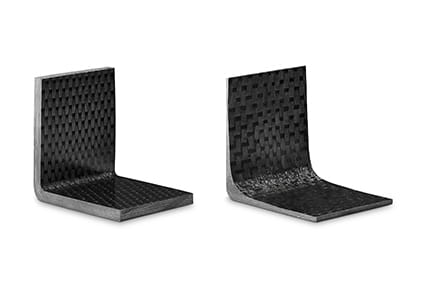
Díky technologii předlisku Ensinger jsou při vytváření úhlů možné také rozdíly v tloušťkách stěn. Podobně jako u rozvětvené větve lze rohovou část pod vysokým napětím zesílit, zatímco v částech, které nejsou pod velkým napětím (např. Na ramenou), lze materiál ušetřit. Výrobní technika se označuje jako proces „tvaru téměř sítě“.
V závislosti na geometrii součásti je díky této technologii možné dosáhnout výrazných úspor materiálu a hmotnosti - při zachování srovnatelné pevnosti a tuhosti.