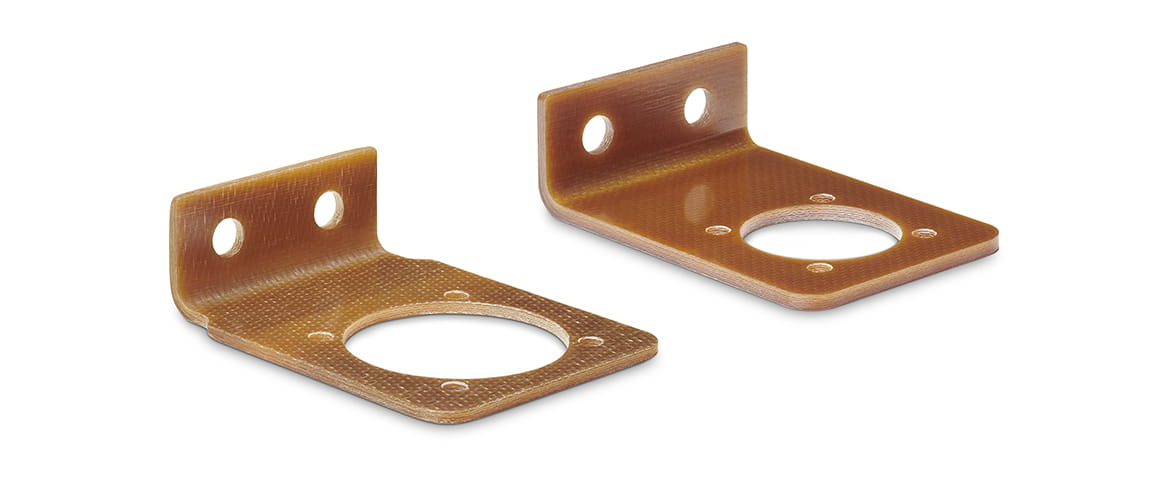
Soportes para conexiones eléctricas enchufables
Construcción liviana en interiores de aviones: componentes fabricados en serie a base de composite
Los materiales livianos y de alta resistencia se han vuelto indispensables para aplicaciones de alta gama en la industria de la aviación. En los aviones de pasajeros, cada kilogramo cuenta, por lo que los metales se sustituyen cada vez más por soluciones basadas en plásticos, también en el diseño de interiores. Los compuestos termoplásticos, en particular, ofrecen a las empresas que equipan aviones una reducción de peso significativa que no compromete sus propiedades mecánicas. Un proyecto de las empresas Bucher Leichtbau y Ensinger muestra que el cambio a composites reforzados con fibra puede proporcionar ventajas técnicas adicionales.
Bucher Leichtbau AG, con sede en Fällanden (Suiza), está especializada en interiores de aviones y equipamiento de automoción. Entre otras cosas, la división de aviación del grupo empresarial desarrolla y produce cocinas y armarios para aviones de pasajeros. Un módulo completo de este tipo puede soportar una carga equivalente a ocho veces su propio peso y debe poder soportar aceleraciones que sean al menos nueve veces superiores a la aceleración gravitacional. Aquí, se hace una distinción entre cargas de vuelo (condiciones de vuelo normales como despegue, aterrizaje, turbulencia) y cargas de aterrizaje de emergencia (aterrizaje de emergencia controlado o despegue interrumpido). La vida útil mínima requerida de los módulos producidos es, por ejemplo, de 25 años para Airbus y Boeing.
Situación inicial
Por razones de seguridad, todos los soportes metálicos para conexiones eléctricas enchufables en la aviación comercial deben estar conectados a tierra. Con estructuras de soporte conductoras eléctricamente en las cocinas de aluminio de Bucher, a menudo es suficiente un tornillo de fijación existente equipado con las medidas necesarias de protección contra la corrosión. Sin embargo, si los montajes de conectores metálicos se colocan en estructuras no conductoras en las cocinas, se requiere un cable adicional para la conexión eléctrica a tierra. Este cable de conexión a tierra se debe asegurar a intervalos regulares, para lo que se precisan roscas de sujeción, pernos espaciadores, abrazaderas de cable y tornillos adicionales.
Además de la entrada de material para el tendido de cables, surgen altos costos de planificación e instalación: el trabajo de diseño incluye hacer una entrada en el diagrama esquemático del circuito; es más, se debe definir una medición de resistencia en el plan de prueba para cada cable de toma de tierra. Esto también debe incorporarse en las directrices de mantenimiento e instrucciones de funcionamiento pertinentes, así como en los documentos de autorización. Durante la producción, se debe registrar la resistencia de contacto y aplicar una capa de protección contra la corrosión en cada conexión a tierra.
El sustituto de composite termoplástico elimina la necesidad de conexión a tierra
El trabajo y los costos involucrados en una conexión a tierra se pueden eliminar por completo si los montajes de conectores previamente hechos de metal se reemplazan por una variante no conductora. Sin embargo, debido a la temperatura de funcionamiento y a los requisitos de seguridad contra incendios, no es posible utilizar un plástico estándar de bajo costo.
La codiciada alternativa técnica debía ser capaz de reemplazar, una a una, una gran cantidad de piezas de chapa de aluminio existentes para minimizar el trabajo y los costes implicados al cambiarlas cuando fueron introducidas. Para satisfacer esta demanda, se requiere un material rígido y de alta resistencia.
Debido a las cantidades relativamente pequeñas de los diferentes soportes de conectores, no se contemplaba una solución con altos costos en herramientas. Las pruebas iniciales con piezas localmente remodeladas hechas de material laminado termoplástico reforzado con fibra no mostraron resultados satisfactorios en las zonas remodeladas.
Trabajando con la división de composite de Ensinger, se encontró rápidamente una solución adecuada basada en composite reforzado con fibra termoplástica. Para el material se eligió un preimpregnado aprobado para la industria de la aviación con fibra de vidrio y una matriz de PEI (polieterimida). Después de una breve fase de optimización, fue posible fabricar las primeras piezas producidas en serie. Debido a las técnicas de producción especializadas, dos de las plantas de Ensinger están involucrados en la elaboración de los soportes para conectores:
En el centro de Otelfingen, los expertos en composite de Ensinger producen piezas semiacabadas en forma angular a partir de los preimpregnados de PEI. A diferencia de los componentes comparables, estos objetos no grabados no se cortan a medida a partir de un laminado grueso y se termoforman después, sino que, utilizando capas individuales de preimpregnación, se comprimen en una herramienta en la forma definida. Entre otras cosas, este proceso ofrece la ventaja de reducir el efecto de recuperación elástica. El mecanizado con control numérico (CNC) de las piezas de composite de fibra se lleva a cabo en Ensinger GmbH en Cham, Baviera.
El departamento de mecanizado de Cham, que se especializa en la producción de piezas de precisión a partir de plásticos termoplásticos de alto rendimiento y materiales composite, es miembro del grupo internacional de mecanizado de Ensinger. Desde los objetos sin grabar angulares producidos en Otelfingen, Ensinger in Cham mecaniza con precisión los montajes de los conectores hasta la especificación del producto final.
Para la mayoría de los soportes de fijación, existen varias versiones con diferentes dimensiones. Gracias al proceso flexible, también es posible producir diseños especiales de alta calidad con contornos o agujeros perforados y con plazos de entrega cortos.
Más simple, rentable y ligero
ANTES DEL MECANIZADO CNC
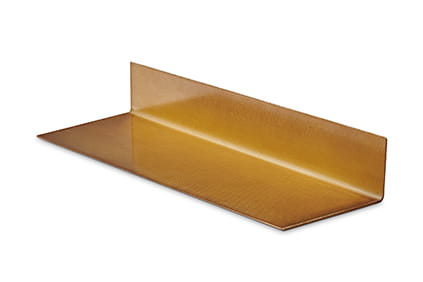
Un objeto sin grabar para un soporte de conexión enchufable se construye a partir de un composite de fibra preimpregnado, aprobado para la industria de la aviación con fibra de vidrio incrustada en una matriz de PEI.
Los soportes de los conectores vienen en versiones de diferentes dimensiones. Gracias a las fibras continuas y alienadas, el material composite termoplástico tiene una resistencia y rigidez significativamente mayores a los plásticos reforzados con fibras cortas.
TECNOLOGÍA DE PREFORMAS
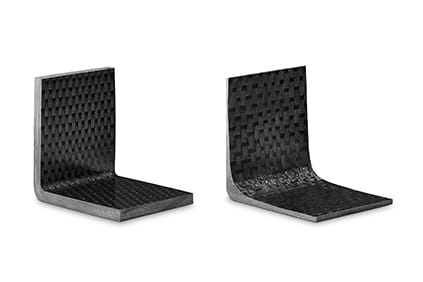
Gracias a la tecnología de preformas de Ensinger, también se pueden producir ángulos con diferente grosor en las paredes. De manera similar a una rama bifurcada, la sección de la esquina sometida a grandes esfuerzos se puede reforzar, mientras que en las secciones que no están sometidos a grandes esfuerzos (por ejemplo, en los brazos), se puede ahorrar material. La técnica de fabricación se conoce como el proceso de “forma casi neta”.
Según la geometría del componente, con esta tecnología es posible un ahorro significativo de material y peso, al tiempo que se mantiene una resistencia y rigidez comparables.