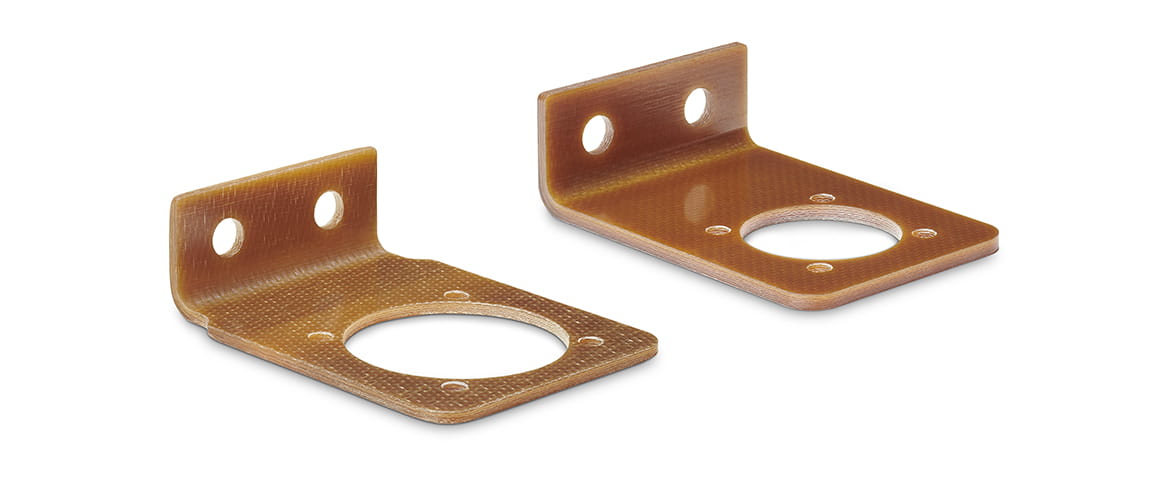
Montagedelen voor elektriche insteekverbindingen
Lichtgewicht constructie in vlieguituiginterieur: Composiet seriegeproduceerde componenten
Lichtgewicht en zeer sterke materiaen zijn onmisbaar geworden voor de high end toepassingen voor de vliegtuigindustie. In passagiersvliegtuigen telt iedere kilo, dit is waarom metalen meer en meer vervangen worden dooorkunststof oplossingen, ook in het interieur ontwerp. Thermoplastische composieten bieden bedrijven die vliegtuigen aankleden een significante gewichtsreductie, zonder dat er van hen geist wordt dat er een compromis gemaakt moet worden in termen van mechanische eigenschappen. Een project door Bucher Leichtbau en Ensinger toont aan dat het wisselen naar vezelversterkte composieten technische voordelen kan bieden.
Bucher Leichtbau AG, met hoofdkantoor in Fällanden (Switzerland), is een specialist voor vliegtuiginterieur en automotive apparatuur. De luchtvaart divisie van de groep ontwikkelt onder andere combuisen en kasten voor passagierstoestellen. Een volledige module van dit type kan 8 keer zijn eigen gewicht herbergen, en moet hier tegen bestand zijn bij een accelaratie van 9G. Hie is een onderscheid getekend vluchtlasten (normale vliegcondities, zoals opstijgen, landen en turbulentie) en noodlandinglasten (gecontroleerde noodlanding afgebroken start) De vereiste minimale levensduur van de geproduceerde modules is 25 jaar voor Airbus en Boeing.
Begin situatie
Vanwege veiligheidsredenen moeten alle metalen montagedelen voor electrische insteekverbindingen geaard zijn. Met electrisch geleidende constructiedelenin the Bucher aluminium combuisen, is een bestaande schroef met de noodzakelijke corrosie bescherming meestal voldoende. Als de metalen connector montagesteunen op niet geleidendende delen van de combuisen geplaatst worden, is een extra kabel voor aarding vereist. Deze aardkabel moet met reguliere intervallen beveiligd worden, waardoor er eisen komen voor additionele bevestigingsdraden, afstandsbouten, kabelklemmen en schroeven.
Naast het extra materiaal voor de kabel input, ontstaan er hoge kosten voor de installatie. Het ontwerpwerk omvat het maken van een extra ingang in het schematische circuit; verder moet er nog een testplan voor iedere grondkabel gedefinieerd worden. Dit moet ook ingevoegd worden in de betreffende onderhoudsrichtlijnen, als ook in de authorisatiedocumenten. Gedurende de produktie moet de contatcweerstand worden vastgelegd en een corrosiebeschermingscoating moet worden toegepast bij iedere aardingsconnectie.
Thermoplastische composieten vervanging zorgt voor geen noodzaak voor aarding
Het werk en de kosten bij een aardingsverbinding kan compleet ovorbodig worden als het connector montagedeel, vroeger uit metaal, vervangen wordt door een niet geleidende variant. Vanwege de gebruikstemperatuur en de brandveiligheidseisen, is dit echter niet mogelijk met het gebruik van een goedkope standaard kunststof.
Het zoeken naar een technisch alternatief moest in staat zijn een groot aanatal aluminium plaatjes een op een te vervangen, om zo kosten en werk te verminderen. Om aan de eisen te voldoen, is een rigide, zeer sterk materiaal vereist.
Vanwege de relatief kleine hoeveelheden verschillende connector montagedelen, was een oplossing met hoge matrijskosten geen optie. De eerste tests met lokaal gevormde delen gemaakt van vezelversterkte thermoplastische materialen toonden geen tevredenstellende resultaten.
Al samenwerkend met Ensinger´s Composieten Divisie werd een passende oplossing op basis van een thermoplastsich vezelversterkt composiet snel gevonden. Een prepeg , goedgekeurd voor de luchtvaartindustrie met glasgevuld en een PEI matriks (polyetherimide) werd gekozen als materiaal. Na een korte optimaliseringsfase was het mogelijk om de eerste series te produceren. Vanwege de specialistische procestechnieken, werden twee van Ensinger´s produktielocaties betrokken bii de productie van de connector montagedelen:
Op de locatie Otelfingen, produceren de composiet experts van Ensinger halffabrikaten delen van de PEI prepegs in een hoekige vorm. Niet zoals vergelijkbare delen worden deze plaatjes niet op maat gesneden uit een dik lamininaat en dan thermisch gevormd, maar worden ze in een vormgeperst, met gebruik van individuele lagen. Naast andere zaken, biedt dit proces het voordeel van verminderen van het terugveer effect. Het CNC verwerken van de vezelcomposieten vond plaats bij Ensinger GmbH in Cham in Bayern.
De Cham verspaningsafdeling , die gespecialiseerd is in de productie van precisie-onderdelen, is deel van Ensinger´s internationale verspaningsgroep. Van de rechthoekige plaatjes geproduceerd in Otelfingen verspaant Ensinger in Cham de connector montagedelen tot de definitieve prooduct specificatie.
Voor de meeste monatfgedelen zijn er verschillende versies met verschillende afmetingen. Dankzij het flexibele proces is het mogelijk om hoge kwaliteit speciale ontwerpen met aftekeningen of geboorde gaten te produceren met korte levertijden.
Simpeler, goedkoper en lichter
Voor het verspanen
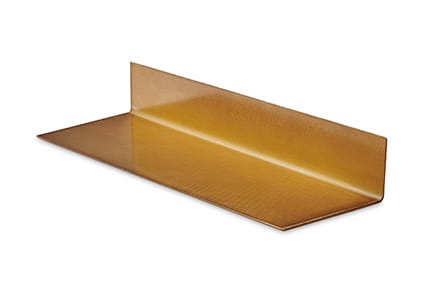
Een plaatje voor een steun voor een insteekconnector is uit een vezelcomposiet prepreg geconstrueerd, is met glasvezel in een PEI matrix goedgekeurd voor de luchtvaartindustrie.
Het connector montagedeel heeft verschillende versies en dimensies. Dankz ij de continue en geordende vezels heeft dit thermoplastisch composiet materiaal een duidelijk hogere sterkte en stijfheid dan kunststoffen die versterkt zijn met korte vezels.
PREFORM TECHNOLOGie
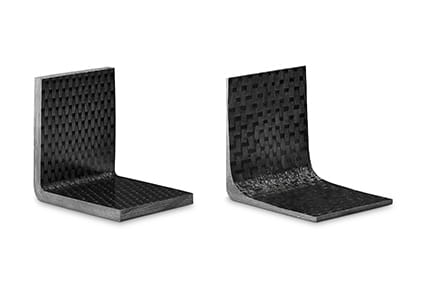
Dankzij Ensinger's preform technologie zijn verschillen in wanddikte mogelijk als er hoeken geproduceerd worden. Gelijk aan een gevorkte tak kan de hoek sektie met hoge spanningen versterkt worden, terwijl in die secties die niet zo onder spanning staan (bv de armen) materiaal kan worden bespaard. De produktietechniek wordt het "bijna netto vorm" genoemd
Afhankelijk van de component geometrie zij grote besparingen met deze technologie mogelijk, terwijl de sterkte en de stijfheid wordt behouden.