Plastic material solutions for the semiconductor industry
Of all the industries in which engineering plastics can help engineers solve design problems, none is more challenging than the semiconductor industry. Our semiconductor industry plastics are designed with the industry's often rigid and demanding environmental concerns in mind. In addition to this, our semiconductor industry specialists work directly with engineers to understand the unique challenges associated with every aspect of the semiconductor manufacturing process - from the beginning of the wafer processing cycle, through chip processing and handling, to packaging.
Each stage of the process offers its own set of difficulties, from extremely high temperatures, to exposure to highly aggressive chemicals, contact with abrasive solvents and environments of plasma under a vacuum. Ensinger has a plastic semiconductor solution to suit every environment and meets the strictest requirements for design and machining tolerance, outgassing, and contamination specifications. Our design solutions cost less than traditional materials, such as ceramics or quartz, and are generally much easier to work with.
Benefits FOR THE Semiconductor industry
Extensive product range, engineering support and testing capabilities
Customer specific, industry and government agency compliance expertise
Strategic vendor alliances with premier resin suppliers worldwide
Solutions for THE Semiconductor Industry
Special materials for CMP
Low outgassing plastics
High temperature plastics
ESD plastics
Chemical resistance
Machinable Plastics for THE Semiconductor Industry
- TECAPEEK ELS nano black
- TECAPEEK CMP natural
- TECASINT 5051 green-grey
- TECASINT 4111 natural
- TECASINT 4011 natural
- TECAPEI natural
Semiconductor Industry CASE STUDIES
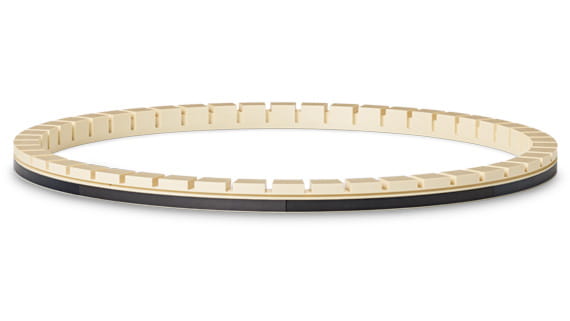
How to meet the numerous requirements of CMP process
A very important step in silicon wafer production, is the Chemical Mechanical Planarization (CMP) process. The trend is towards larger wafer sizes, smaller chips with narrower line widths and feature sizes. The challenge is to find a material with the desired characteristics, as the CMP process requires components made of highly qualified materials. In close cooperation with customers, we have specialised in developing materials that meet these requirements.