Flow sensors with EMST
Revolutionary manufacturing technology: PEEK-based flow sensors
Flow sensors are typically manufactured on conventional substrates such as ceramics or silicon, especially for applications requiring lithographic techniques. For flexible sensors, such as temperature sensors or thermal flow sensors, polymer-based substrates are sometimes used, offering some advantages in terms of heat capacity, thermal conductivity and electrical insulation. However, the polymer solutions used to date have disadvantages in terms of chemical and thermal resistance, and are often unable to withstand the intensive lithographic processes of traditional applications.
EMST offers a completely new approach. By using TECACOMP PEEK LDS, a high performance plastic manufactured in-house, we're the first to combine the advantageous chemical and thermal properties of the high performance plastic with our newly developed manufacturing technology. Our PEEK-based wafer, TECAWAFER PEEK LDS, enables the production of high performance and versatile thermal flow sensors without a cleanroom environment - efficient, flexible and customisable even in small quantities.
In general, PEEK has a lower thermal conductivity than ceramic or silicon-based substrates, which improves sensor sensitivity. TECAWAFER PEEK LDS offers additional advantages: The functionalisability of the substrate allows the production of customised solutions. Coatings, beyond the traditional options such as gold, nickel and copper, extend the functionalisation possibilities and create entirely new solutions for flow sensor manufacturers. In terms of integration, our PEEK-based solution offers flexible molding options to seamlessly integrate custom flow sensors into the specific requirements of the application. Our technology allows for unparalleled customisation of microsystems, enabling unique functions, shapes and quantities – even in low volumes. We can tailor functions, shapes, quantities and sizes to meet your specific requirements.
With this in mind, we have combined our expertise with our partner Hahn Schickard to develop and manufacture a thermal flow sensor based on TECACOMP PEEK LDS.
Functionalisation
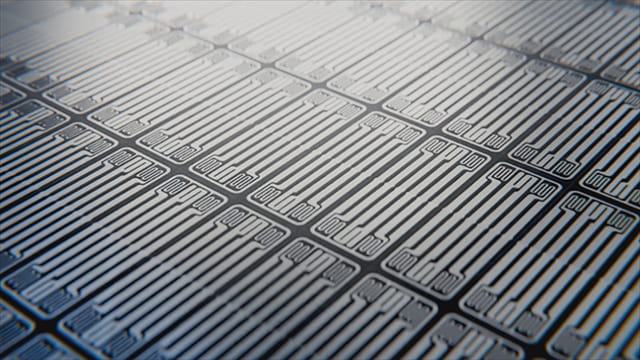
Integration
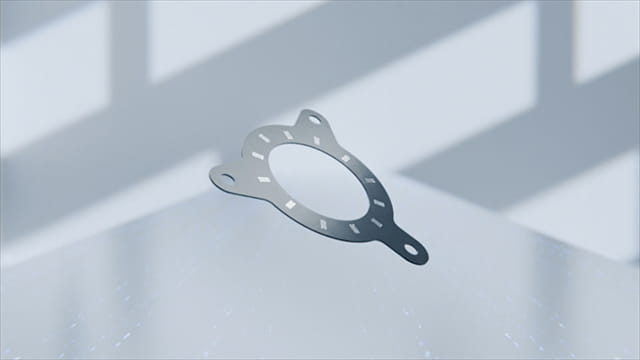
Individualisation
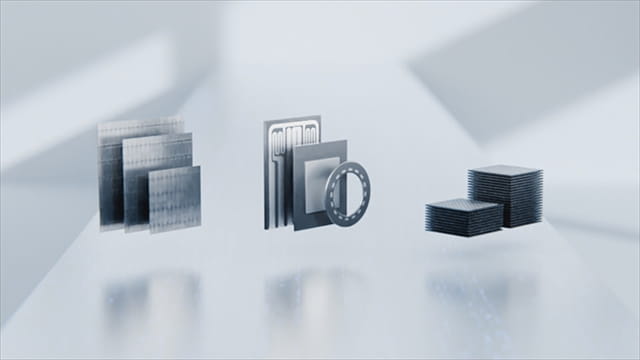
Accurate flow measurement: Thermal flow sensor from Hahn Schickard & EMST
The development of the PEEK-based thermal flow sensor by EMST offers a promising solution for precise flow measurement. With a compact sensor element containing a centred heater and two temperature sensors, accurate detection of flow direction and flow rate is possible.
The use of high quality materials, such as nickel-chromium for the heater and nickel for the sensors, and precise manufacturing techniques, such as CNC milling and the LPKF-LDS process, ensure high accuracy and reliability of the sensor. The multiplication of the layout on a wafer enables efficient mass production and thus cost-effective sensor production compared to traditional substrate solutions. The subsequent characterisation of the sensor shows a good response to different flow rates and confirms its suitability for applications in the 0-3 bar measurement range.
Overall, the development of this thermal flow sensor represents a significant step forward, offering a wide range of applications in both research and industry, and contributing to more accurate and efficient flow measurement.
Flow sensor process chain
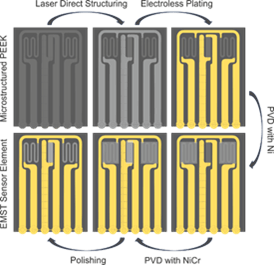
Functional Sensors for Industrial Applications
"At Ensinger Microsystems Technology, we combine inventive materials, precise manufacturing and smart technologies to create powerful systems that drive industries forward."
Dr. Sebastian Bengsch, Inventor and Start Up Lead EMST
Ready to rethink flow sensor manufacturing?
We are ready for your flow sensor application. Contact us to discuss your possibilities with EMST.