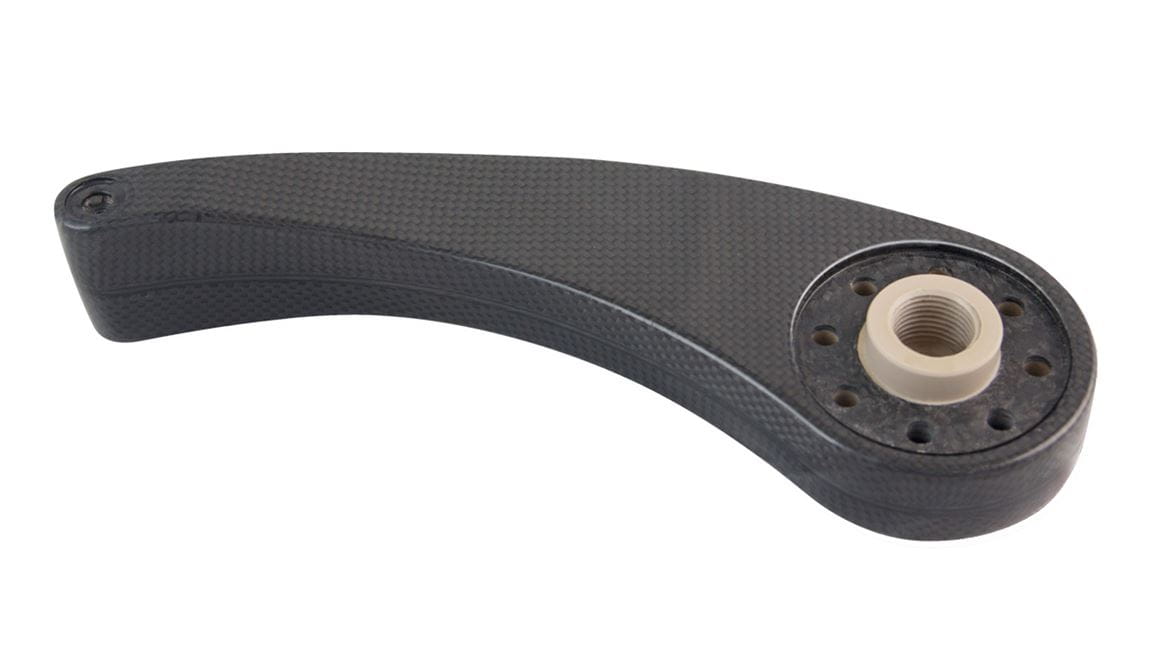
Composite robotic arm
In this case study, Loson and Ensinger cooperated to improve the performance of a robotic arm used in a Delta robot for food packaging lines. Such fast and accurate machines are used in factories for picking and packaging thanks to their speed that makes it possible, in some cases, to perform up to 300 picks per minute.
Carbon fibre composite parts (in this case carbon woven fabric in an epoxy matrix) are designed and produced to reduce weight and inertia, preserving high mechanical properties typical of high quality metal alloys. Although lightness is one of the main targets, heavy metal inserts (steel, aluminium or, in few cases, titanium) are normally necessary to connect carbon fibre composite parts to other mechanical components, so the benefit of the carbon fibre is partially reduced.
Fig. 1 shows a robotic arm for a machine in the food packaging industry: of a total weight of about 300 g, more than 80 g (27%) are accounted for by aluminium inserts, so the effort to reduce the weight of the part (to reduce inertia) is partly compromised. Also, in harsh environments, where aggressive acids/bases are used for cleaning (e.g. food packaging lines), this configuration is subject to a high risk of salt corrosion or galvanic coupling corrosion.
Aluminium
The idea is to substitute an insert made of aluminium (or another metal, and thus even heavier) using a high-performance polymer in order to reduce weight, reduce the risk of corrosion and, at the same time, guarantee the high mechanical performance required by the application.
Metal inserts are generally bonded to composite parts using two-component epoxy glues, or are directly incorporated in the composite frame using the resin of the polymeric matrix as bonding agent.
Unfortunately, looking at the literature, the bonding strength between a polymeric insert and the composite part cannot guarantee the same level of adhesion, as seen, for example, in Table n.1. This graph shows that the shear strength of a connection by gluing of different thermoplastic polymers is generally well below the threshold of 6 MPa, generally considered to be the minimum for "structural" bonding.
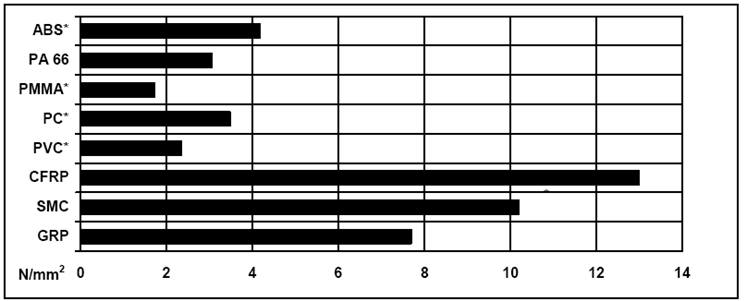
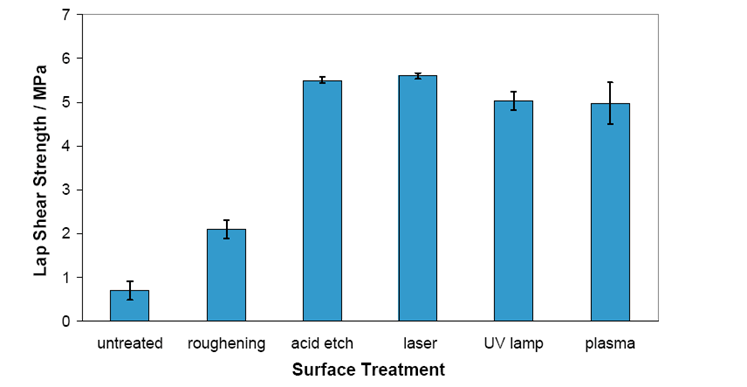
As always, when replacing a metal with a plastic, component design needs to be analysed and adapted to the new material after identifying possible critical aspects such as tolerances, structural design and connections.
The adhesion of epoxies to PEEK is always much lower than to metal. For example, Table n. 2 shows the PEEK on PEEK bonding with different surface treatments and under various conditions, and underlines the low performances of bonded polymer surfaces.
In the case of this composite robotic arm, the original insert design did not grant secure adhesion of the component to the CRFP matrix, with the risk of relative rotation between the insert and the arm.
To overcome the low performance of the glue and avoid the relative rotation of the components, a mechanical connection between TECAPEEK natural insert and carbon fibre composite part was designed and produced. As shown in the cross-section in drawing n.2, some undercuts are machined in the TECAPEEK natural insert so that it can be safely incorporated into the carbon fibre composite part during the lamination process. The undercuts of the inserts are completely filled with the laminated composite material to avoid any relative rotation of the two components.
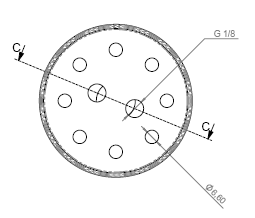
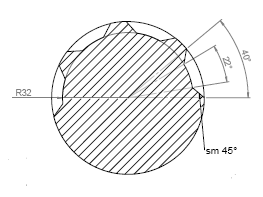
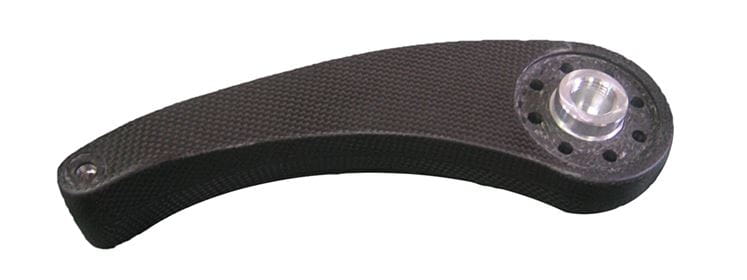
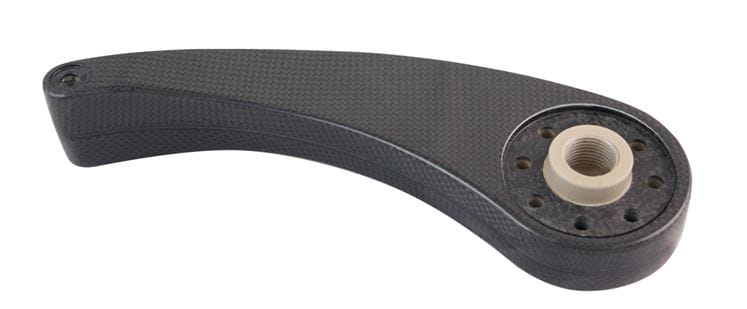
A perfectly interchangeable solution for the original composite robotic arm was developed. The component was enhanced by:
- Use of inserts machined in high-performance plastic (TECAPEEK natural), which increases the ratio performance/weight ratio of the assembly compared to aluminium inserts.
- Upgrade of component design including machined undercuts, filled directly with the composite matrix during the lamination procedure, to avoid the use of the glue. This solution avoids unwanted relative rotation of the components.
- Protection from galvanic and chemical corrosion thanks to the absence of metals.
With this solution, the total weight of the part was further reduced by almost 15%, theoretically allowing faster and safer operation of the Delta robot thanks to the lower moment of inertia.
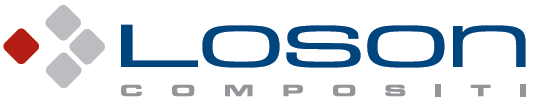