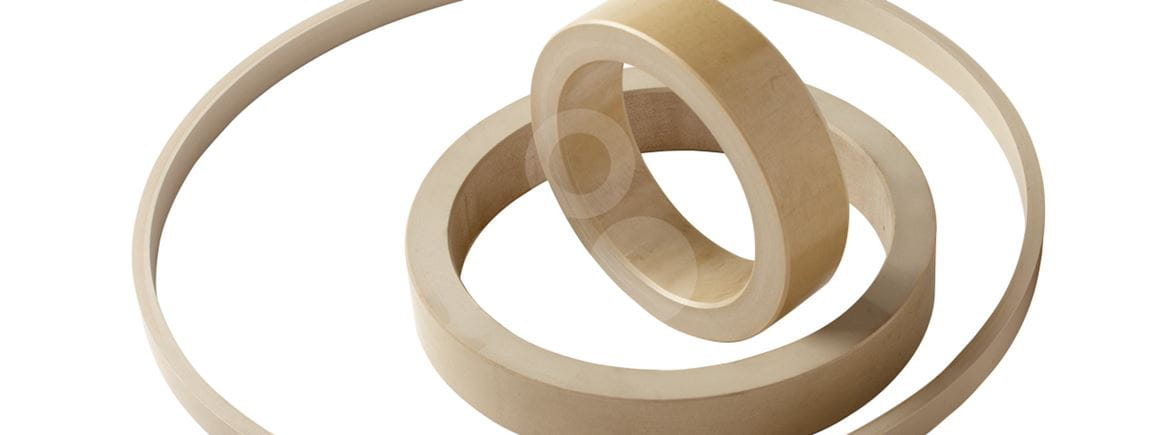
Seals and back up rings for the Oil and Gas industry
In the oil and gas industry, oil seals are used to prevent dust, dirt, water and any other harmful substances from entering and damaging machinery. Seals are a vital component to help protect various components such as tight-fitting ball, sleeve and roller bearings. It is vital to ensure the most appropriate material is used to produce seals depending on the environment they will be operating in, as different environments may require materials with different degrees of resistance to chemicals and temperatures.
Demanding conditions
In every aspect of oil and gas exploration, choosing the most suitable materials is critical for effective sealing applications. The oil and gas production process requires sealing systems capable of operating up to potentially high pressures and temperatures. Higher temperatures and higher temperature exposure has created a need for materials that can withstand these demanding elements. These extreme conditions require materials that compliment, or back up elastomers in attaining the proper sealing effect. Typical sealing materials used within these systems offer the temperature and chemical portfolio, however, their relatively poor mechanical properties can lead to extrusion through seal gaps during operation. Therefore, the need to reduce gaps in sealing is essential, in order to reduce downtime and costly maintenance, which can be a challenge depending on the environment.
Room for improvement
High performance thermoplastics are commonly used in sealing and back up applications in the oil and gas industry due to the properties they hold. PTFE and PPS are often used for sealing applications as they have exceptional chemical resistance and are suited well for harsh environments, however where creep is a factor, PEEK may be more suited as PTFE has a low coefficient of friction.
PEEK is often favored for sealing applications as it is able to withstand extreme temperatures and chemicals often found in high temperature and high pressure environments. Ensinger TECAPEEK (PEEK) has been proven to have the mechanical properties necessary to be used as a back-up ring to these seals, or even potentially as a seal itself. Additional confidence is given as Ensinger's TECAPEEK products are able to achieve compliance for use in highly demanding oil and gas applications according to ISO 23936-1:2009 and NORSOK M-710, Edition 3.
Choosing to use plastics for this application can be beneficial in a number of ways. The use of thermoplastics can result in less downtime and maintenance whilst also displaying improved reliability. Therefore, customers can benefit from the ability to reach new depths in the exploration of new reservoirs that may have been previously unattainable.
PEEK is often favored for sealing applications as it is able to withstand extreme temperatures and chemicals often found in high temperature and high pressure environments. Ensinger TECAPEEK (PEEK) has been proven to have the mechanical properties necessary to be used as a back-up ring to these seals, or even potentially as a seal itself. Additional confidence is given as Ensinger's TECAPEEK products are able to achieve compliance for use in highly demanding oil and gas applications according to ISO 23936-1:2009 and NORSOK M-710, Edition 3.
Choosing to use plastics for this application can be beneficial in a number of ways. The use of thermoplastics can result in less downtime and maintenance whilst also displaying improved reliability. Therefore, customers can benefit from the ability to reach new depths in the exploration of new reservoirs that may have been previously unattainable.
high performance thermoplastics for Seals and Back up rings
Furthermore, mechanical properties of Ensinger plastics can also be enhanced with the introduction of fillers like glass and carbon reinforcement which also gives advantages over other materials.