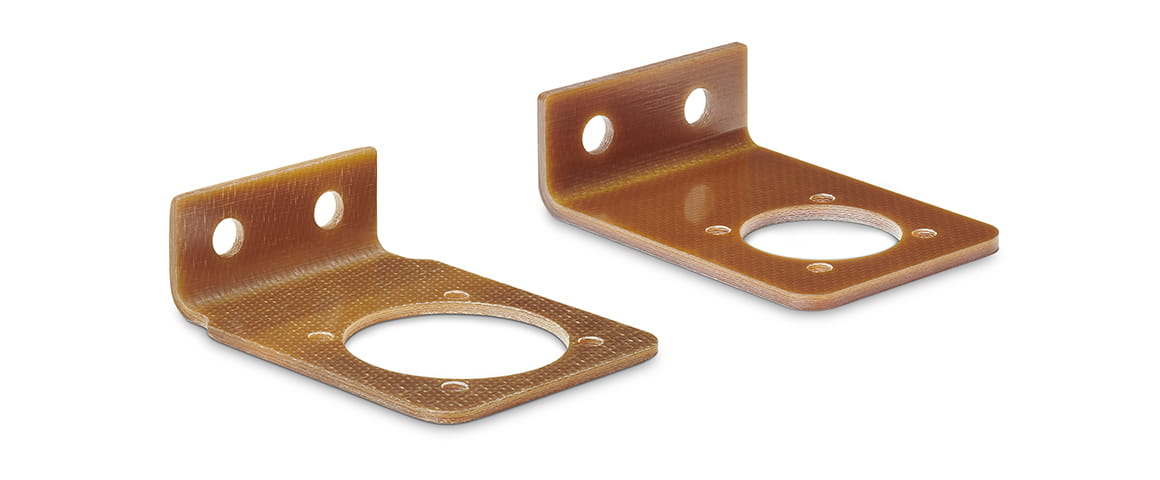
Mountings for electrical plug-in connections
Lightweight construction in aeroplane interiors: composite-based series-produced components
Lightweight and high-strength materials have become indispensable for high-end applications in the aviation industry. In passenger aircraft every kilogram counts, which is why metals are increasingly being replaced with plastics-based solutions, especially in interior design. Thermoplastic composites, in particular, offer companies tasked with designing airplanes significant weight reduction without requiring them to make compromises in terms of mechanical properties. A project co-managed by Bucher Leichtbau and Ensinger shows that making the switch to fibre-reinforced composites can provide additional technical advantages.
Bucher Leichtbau AG, headquartered in Fällanden (Switzerland), is a specialist for aircraft interiors and automotive equipment. Among other things, the aviation division of the corporate group develops and produces galleys and cabinets for passenger aircraft. A full module of this type can accommodate a load corresponding to eight times its own weight and has to be able to withstand accelerations that are at least nine times that of gravitational acceleration. Here, a distinction is drawn between flight loads (normal flight conditions such as take-off, landing and turbulence) and emergency landing loads (controlled emergency landing or aborted take-off). The required minimum operating life of the modules produced, for example is 25 years for Airbus and Boeing.
Initial situation
For safety reasons, all metal mountings for electrical plug-in connections in commercial aviation must be grounded. With electrically conductive supporting structures in the Bucher aluminium galleys, an existing fastening screw equipped with the necessary corrosion protection measures is often sufficient. If, however, the metal connector mountings are positioned on non-conductive structures in the galleys, an additional cable is required for the electrical grounding. This grounding cable must be secured at regular intervals which drives a requirement for additional fastening threads, spacer bolts, cable clamps and screws.
In addition to the material input for the cable routing, high costs arise for planning and installation: The design work includes making an entry in the schematic circuit diagram and what is more, a resistance measurement must be defined in the test plan for every grounding cable. This must also be incorporated into the relevant maintenance guidelines and operating instructions, as well as into the authorization documents. During production, the contact resistance must be recorded and a corrosion protection coating be applied with every ground connection.
Thermoplastic composite substitute removes the need for Grounding
The work and costs involved in a ground connection can be completely eliminated if the connector mountings previously made from metal are replaced by a non-conductive alternative material. Because of the operating temperature and fire safety requirements, however, it is not possible to use a low-cost, standard plastic.
The alternative needed to be capable of replacing a large number of existing sheet aluminium parts one-to-one so as to minimise the work and costs involved in switching when they were introduced. For this demand to be met, a rigid, high-strength material was required.
Owing to the relatively small quantities of the different connector mountings, a solution with high tool costs such as an injection molded part was not an option. Initial trials with locally redesigned parts made from fibre-reinforced, thermoplastic sheet material also did not show satisfactory results.
Working with Ensinger’s Composite division, a suitable solution based on thermoplastic fibre-reinforced composite was quickly found. A prepreg approved for the aviation industry with glass fibre and a PEI matrix (polyetherimide) was chosen. After a brief optimisation period, it was possible to manufacture the first series-produced parts. Because of the special processing techniques, two of the Ensinger’s sites are involved in the production of the connector mountings:
At the Otelfingen site, Ensinger's composite experts produce semi-finished parts in an angular shape from the PEI prepregs. Unlike comparable components, these blanks are not cut to size from a thick laminate and thermoformed but, using individual prepreg layers, pressed in a tool into the defined form. Among other things, this process offers the advantage of reducing the springback effect. The CNC processing of the fibre composite parts takes place at Ensinger GmbH in Cham in Bavaria.
The Cham machining department, which specialises in the production of precision parts from thermoplastic high-performance plastics and composite materials, is a member of Ensinger’s international machining group. From the angular blanks produced in Otelfingen, Ensinger in Cham machines the connector mountings to final product specification.
For most fastening brackets there are several versions with different dimensions. Thanks to the flexible process, it is also possible to produce high-quality, special designs with contours or drilled holes and with short lead times.
Simpler, more cost-effective, and lighter
BEFORE CNC PROCESSING
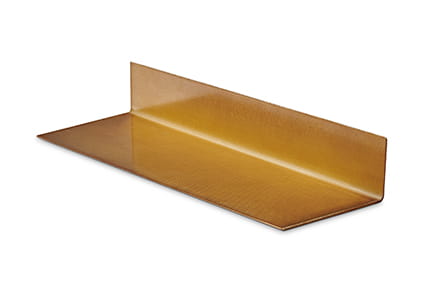
A blank for a bracket for a plug-in connection is constructed from a fibre composite pre-preg, approved for the aviation industry with glass fibre which is embedded in a PEI matrix.
The connector mountings come in versions with different dimensions. Thanks to the continuous, straightened fibres, the thermoplastic composite material has significantly higher strength and rigidity than short fibre-reinforced plastics.
PREFORM TECHNOLOGY
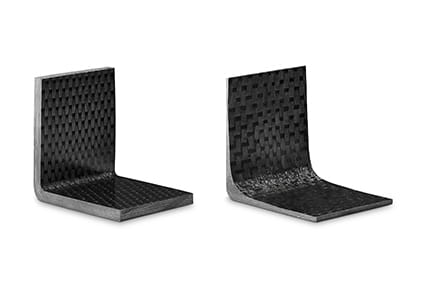
Thanks to Ensinger's preform technology, differences in wall thicknesses are also possible when producing angles. So similar to a forked branch, the corner section under high stresses can be reinforced, while in the sections which are not under high stresses (e.g. on the arms), material can be saved. The manufacturing technique is referred to as the ‘near net shape’ process.
Depending on the component geometry, significant material and weight savings are possible with this technology – whilst maintaining comparable strength and rigidity.