Rethinking pressure sensor manufacturing with EMST
Pressure sensors are used in a wide range of applications: in air suspension systems in the automotive industry, in compressed air systems in railway technology or in high-precision pump systems in medical technology. As different as the applications may be, they all have one thing in common: pressure sensors are microsystems, i.e. micromechanical (or microoptical) components that combine and integrate microelectronic components into a complex system.
Pressure sensors in systems or machines measure the pressure of liquids or gases. They convert the mechanical force that the pressure exerts on a specific surface, usually the pressure sensor membrane, into an electrical signal. When pressure is applied to the membrane, it is deformed. This strain can be accurately measured and used to calculate the actual pressure applied. Pressure sensors therefore play a crucial role in monitoring and controlling processes and systems.
Design of lithography-based pressure sensors with strain gauge bridges
Limitations of conventional sensor manufacturing: sensor membranes
A revolution in pressure sensor manufacturing with EMST
Ensinger Microsystems Technology (EMST) is changing the way pressure sensors are manufactured. We do away with corrosive chemicals, complex assembly methods and complicated process steps that consume unnecessary resources. Our newly developed technology, based on the high-performance plastic PEEK, enables pressure sensors to be manufactured much more efficiently and with fewer resources – with additional benefits in terms of functionalisation, integration and customisation.
In our newly developed process chain, the structures of the sensor meander are mapped onto a wafer-shaped substrate using special injection moulding processes without the need for lithography. The functionalisation of the substrate and the resulting sensor structures are created by PVD coating and then exposed. The sensor membrane can now be directly imaged on the backside during the injection moulding process or subsequently thinned to the previously defined thickness on the backside by high-precision milling. The thickness, material properties and diameter of the diaphragm define the deflection and resulting pressure range.
Fully Integrated Differential Pressure Sensors with EMST
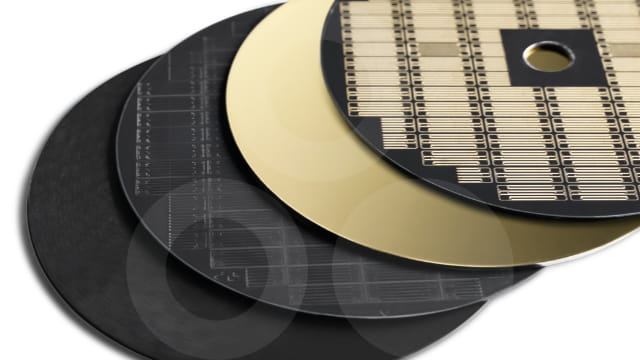
Our current focus is on fully integrated differential pressure sensors. Our newly developed process chain is being successfully used to set up different differential pressure sensor systems and to analyse different diaphragm thicknesses and diameters for different pressure ranges.
Pressure ranges from the low single digit bar range to the high double digit bar range can be resolved.
Innovative pressure sensor solutions from EMST: Integration & customisation on an unprecedented scale
But EMST goes one step further. In addition to simplifying the process chain and conserving resources in the production of pressure sensors, our newly developed production technology offers an unprecedented degree of customisability – for individual pressure sensors that are precisely tailored to your requirements. Sensor formats & placements, load sizes, quantities and functions can be adapted to the application without major technical and financial effort. The high degree of freedom also makes it possible to integrate the sensors into applications that were previously unthinkable. The TECACOMP PEEK LDS material we use also enables innovative contacting of the sensor using the laser direct structuring process.
We would be happy to advise you on your individual pressure sensor solution with EMST.