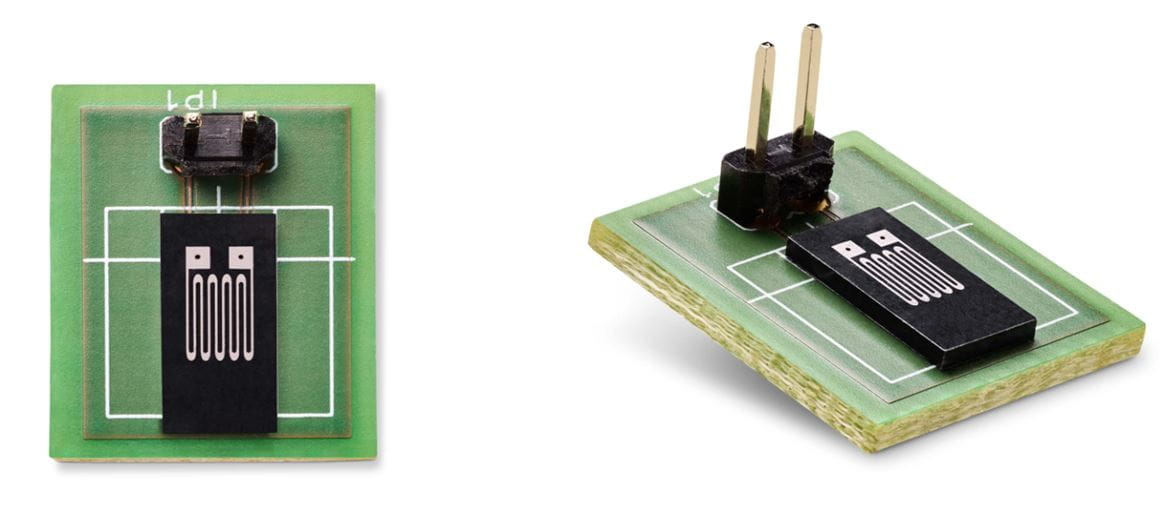
Production of Sensor Systems made Easy, Fast and Cost-effective
With Ensinger Microsystems, we offer a new way of manufacturing sensor systems. Instead of time-consuming and cost-intensive production in a clean room environment, our concept of structuring with plastic injection moulding enables a much simpler and cheaper production and assembly. This makes it possible to manufacture microtechnological systems with less financial and technological effort with similar precision as conventionally manufactured microsystems.
Easy, fast and cost-effective manufacturing and assembly - without the need for a cleanroom environment
Highly qualified experts accompany you at every point of the value-added process - from the compound to the finished sensor system
Individual solutions for your application: magnetic field sensors, pressure sensors, CO2 sensors and numerous other applications are possible
We not only offer over 50 years of experience in the development and processing of thermoplastic high-performance plastics. Our experts for microsystems accompany your project to every point of the value chain. This is how we ensure the highest quality - from the compound to the finished component.
Innovative materials and manufacturing processes
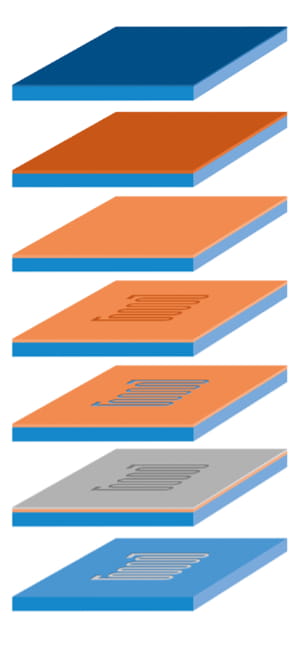
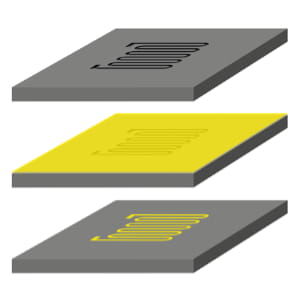
The substrates pre-structured with this process consist of a laser-direct-structurable (LDS) high-temperature thermoplastic TECAPEEK LDS. The combination of the pre-structuring of the substrate, the 3D capability of injection moulding and the functionalisation of the substrate now enable a significant reduction in the process chain compared to the conventional production of microsystems, as well as a reduction in the back-end processes and a simplification of complicated contacting.
In addition, the combination of this process chain with the LDS process known from MID technology (Mold Interconnect Device) opens up backside contacting, which significantly simplifies subsequent assembly compared to conventional silicon substrates and avoids possible wire contacting. Accordingly, the manufacturing approach presented requires a lower vertical range of manufacture. Investments in machine technology and possible clean room infrastructure are significantly reduced.
Sensor Applications & Industries
- Pressure Sensors
- Strain Gauges, Pressure or Temperature Sensors
- CO2 Sensors
- Vibration Sensors
- Current Sensors
- Magnetic Field Sensors
- Magnetoresistive Sensors